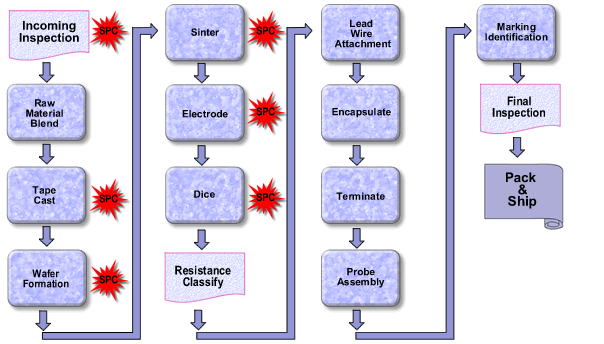
El proceso de fabricación del termistor NTC se puede dividir en: Inspección de Entrada – Mezcla de Materia Prima – Formado de Cinta – Formación de Disco – Sinterizar – Electrodo – Dado – Clasificación de Resistencia – Fijación del Cable de Conducción – Encapsular – Terminar – Ensamblaje de Sonda – Identificación de Marcado – inspección final – Empacar y Enviar .
1. Inspección de Entrada
Todos los materiales primarios se inspeccionan al recibirlos para verificar si sus propiedades físicas y eléctricas son aceptables. Asignar un ID# único y usarlo para la trazabilidad por lotes.
2. Mezcla de Materiales Primarios
La fabricación de termistores NTC comienza con la mezcla precisa de materiales primarios en soluciones de ligantes orgánicos. Estos materiales primarios son óxidos metálicos en polvo, como manganeso, níquel, cobalto y óxido de cobre. También se añaden otros estabilizadores a la mezcla. El óxido y el ligante se combinan utilizando una técnica de proceso húmedo llamada molienda por bolas. En el proceso de molienda por bolas, los materiales se mezclan y el tamaño de partícula del polvo de óxido se reduce. La mezcla homogénea resultante tiene la consistencia de una pasta espesa. La composición exacta de varios óxidos metálicos y estabilizadores determina las características de resistencia-temperatura y la resistividad de los componentes cerámicos cocidos.
3. Colada en Cinta
La "masa" se distribuye sobre una hoja transportadora plástica en movimiento utilizando tecnología de cuchilla de doctor. La espesor exacto del material se controla ajustando la altura de la espátula sobre la hoja transportadora plástica, la velocidad de la hoja transportadora y ajustando la viscosidad de la masa. El material de fundición se seca sobre una banda de fundición plana a través de un horno túnel largo a alta temperatura. La cinta resultante "verde" es maleable y fácil de formar. Luego se realiza una inspección y análisis de calidad en la cinta. El grosor de la cinta termistora varía entre 0,001" y 0,100", dependiendo de las especificaciones específicas del componente.
4. Formación de wafer
La cinta está lista para ser formada en discos. Cuando se necesitan materiales delgados, simplemente corte la cinta en pequeños cuadrados. Para discos más gruesos, corte la cinta en cuadrados y apílelos uno sobre otro. Estos discos apilados luego se laminan juntos. Esto nos permite producir discos casi del grosor requerido. Luego, el disco pasa por pruebas adicionales de calidad para asegurar una alta uniformidad y calidad. Posteriormente, el disco se somete a un ciclo de eliminación del ligante. Este método elimina la mayor parte del ligante orgánico del disco. Con el fin de evitar un estrés físico adverso en el disco del termistor, se mantiene un control preciso de tiempo/temperatura durante el ciclo de quema del adhesivo.
5. Sinter
La wafer se calienta a una temperatura muy alta en una atmósfera oxidante. A estas altas temperaturas, los óxidos reaccionan entre sí y se funden para formar una matriz cerámica de espinela. Durante el proceso de sinterización, el material se densifica hasta un nivel predeterminado, y se permite que los límites de grano de la cerámica crezcan. Mantenga un perfil de temperatura preciso durante el proceso de sinterización para evitar fracturas de la wafer y asegurar la producción de cerámicas terminadas que puedan producir piezas con características eléctricas uniformes. Después de la sinterización, se inspecciona nuevamente la calidad de la wafer y se registran las características eléctricas y físicas.
6. Electrodo
El contacto ohmico con los discos de cerámica se obtiene utilizando materiales de electrodos de película gruesa. El material es generalmente plata, paladio-plata, oro o platino, dependiendo de la aplicación. El material del electrodo consiste en una mezcla de metal, vidrio y varios disolventes, y se aplica a las dos superficies opuestas de un disco o chip mediante serigrafía, pulverización o pincelado. El material del electrodo se hornea sobre la cerámica en el horno de cinturón de película gruesa, y se forma la unión eléctrica y la combinación mecánica entre la cerámica y el electrodo. Luego se verifica el disco metализado y se registran sus propiedades. Un control preciso en el proceso de electrodo asegura que los componentes producidos a partir de discos tendrán una excelente fiabilidad a largo plazo
7. Dados
La sierra de corte de semiconductores de alta velocidad se utiliza para cortar el chip en pequeños chips. La hoja de sierra utiliza una hoja de diamante y puede producir un gran número de muertes extremadamente uniformes. El termistor resultante puede ser tan pequeño como 0,010 “a 1000”. La diferencia de tamaño del chip en un conjunto de chips de termistor es prácticamente imposible de medir. Un termistor típico puede producir miles de chips de termistor. Después del corte, se limpia el chip y se verifican las dimensiones y características eléctricas. Las inspecciones eléctricas incluyen la determinación de valores de resistencia nominales para aplicaciones específicas, características de temperatura-resistencia, rendimiento de producción y aceptabilidad del lote. La resistencia y las características de temperatura-resistencia se miden con precisión dentro de 0,001 °C utilizando un control de temperatura preciso.
8. Clasificación de Resistencia
Todos los termistores se prueban para verificar sus valores de resistencia adecuados, generalmente a 25 °C. Estos chips suelen probarse automáticamente, pero también se pueden probar manualmente según la producción y las especificaciones. El procesador de chips automático está conectado a un dispositivo de prueba de resistencia y una computadora programada por el operador para colocar el chip en diversas áreas de memoria dependiendo de su valor de resistencia. Cada procesador de chips automático puede probar 9000 piezas por hora de manera muy precisa.
9. Adjuntar Cable de Conexión
En algunos casos, los termistores se venden en forma de chips y no requieren patas, pero en la mayoría de los casos se necesitan patas. El chip del termistor se conecta a las patas mediante soldadura o por contactos de presión en el paquete de diodo. Durante el proceso de soldadura, el chip del termistor se coloca en el marco de la pata, que depende de la tensión del resorte del alambre para mantener el chip durante el proceso de soldadura. Luego, la ensambladura se sumerge en una olla con estaño fundido y se retira. La tasa de impregnación y el tiempo de residencia se controlan precisamente para evitar un exceso de impacto térmico en el termistor. También se utilizan fluxes especiales para mejorar la soldabilidad sin dañar el chip del termistor. El estaño se adhiere a los electrodos del chip y a las patas para proporcionar una unión firme entre el alambre y el chip. Para el termistor del tipo de paquete “DO-35” de diodo, el chip del termistor se mantiene entre las dos patas de manera axial. La manga de vidrio se coloca alrededor del componente y se calienta a alta temperatura. El vidrio se derrite alrededor del chip del termistor y se sella a la pata. Por ejemplo, en una estructura de diodo, la presión ejercida por el vidrio sobre el módulo proporciona el contacto necesario entre el alambre de la pata y el chip del termistor.
Los cables utilizados para termistores suelen ser de cobre, níquel o aleación, generalmente con recubrimiento de estaño o soldadura. En algunas aplicaciones, se pueden utilizar materiales conductores de aleación con baja conductividad térmica donde se requiera aislamiento térmico entre el termistor y el conductor. En la mayoría de las aplicaciones, esto permite que los termistores respondan a los cambios de temperatura más rápidamente. Después de la unión, verifique el enlace entre el cable y el chip. Una interfaz de soldadura sólida ayuda a garantizar la fiabilidad a largo plazo del termistor terminado.
10. Encapsular
Para proteger los termistores del ambiente de funcionamiento, la humedad, el ataque químico y la corrosión por contacto, los termistores con cables están generalmente recubiertos con un revestimiento protector conformado. El sellador suele ser una resina epoxi con alta conductividad térmica. Otros selladores incluyen silicona, cemento cerámico, pintura, poliuretano y manga retráctil. Los sellantes también ayudan a garantizar una buena integridad mecánica del equipo. La respuesta térmica del termistor debe considerarse al elegir materiales de embalaje. En aplicaciones donde la respuesta térmica rápida es crítica, se utilizan películas de selladores con alta conductividad térmica. Donde la protección ambiental es más importante, se puede seleccionar otro sellador. Los selladores como la resina epoxi, el gel de sílice, el cemento cerámico, la pintura y el poliuretano generalmente se aplican por impregnación y se curan a temperatura ambiente o se colocan en un horno a temperaturas elevadas. Se utiliza un control preciso de tiempo, temperatura y viscosidad durante todo el proceso para asegurar que no se desarrollen poros o otras deformidades.
11. Terminar
Los termistores suelen estar equipados con terminales conectadas al extremo de sus bornes. Antes de aplicar la terminal, se despoja adecuadamente la isolación del cable para ajustarlo al terminal especificado. Estas terminales se conectan a los cables utilizando una máquina de aplicación especializada. Las terminales luego pueden insertarse en una carcasa de plástico o metal antes de ser entregadas al cliente.
12. Ensamblaje de sonda
Por razones de protección ambiental o mecánica, los termistores suelen estar inmersos en el caso de la sonda. Estas cubiertas pueden fabricarse con materiales como epoxi, vinilo, acero inoxidable, aluminio, latón y plástico. Además de proporcionar un montaje mecánico adecuado para los elementos termistor, la carcasa los protege del entorno al que están expuestos. La selección correcta de materiales de cable, aislamiento del cable y encapsulado resultará en un sellado satisfactorio entre el termistor y el entorno externo.
13. Identificación de Marcado
El termistor terminado puede marcarse para una identificación fácil. Esto puede ser tan simple como puntos de color o más complejo, como códigos de fecha y números de pieza. En algunas aplicaciones, se pueden agregar colorantes al recubrimiento del cuerpo del termistor para obtener un color específico. Los puntos de color suelen agregarse al termistor mediante un proceso de impregnación. Use un marcador para generar etiquetas que requieran caracteres alfanuméricos. Esta máquina solo utiliza tinta permanente para marcar las piezas. La tinta se solidifica a una temperatura elevada.
14. Inspección Final
Todos los pedidos completados se inspeccionarán en busca de defectos físicos y eléctricos bajo una base de 'cero defectos'. Todos los parámetros se verifican y registran antes de que el producto salga de la fábrica.
15. Embalar y Enviar Todos los termistores y componentes se empaquetan cuidadosamente y serán utilizados por los clientes.