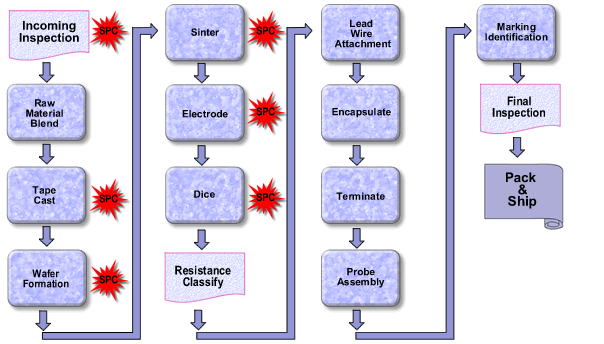
NTC-termistor produsjon kan deles opp i: Innkommende inspeksjon – Blanding av råmaterialer – Båndforming – Waferformering – Sintering – Elektrode – Terning – Motstandsoppgave – Festet av ledertråd – Kapslering – Avslutning – Sømningsmontasje – Merkemålidentifisering – sluttvurdering – Pakke og levering .
1. Innkommende inspeksjon
Alle råmaterialer blir inspisert ved mottak for å verifisere om deres fysiske og elektriske egenskaper er akseptable. Tildel en unik ID# og bruk den til å spore batchen.
2. Blanding av Råmaterialer
Framstillingen av NTC-termistorer begynner med nøyaktig blanding av råmaterialer i organiske binderløsninger. Disse råmaterialene er pulverformete overganger av metalloksid'er som manganes, nikkel, kobber og koboltoksider. Andre stabilisatorer legges også til blandingen. Oksidene og bindemidlet kombineres ved hjelp av en vetskjemisk prosess kalt ballmaling. I ballmalingsprosessen blander materialet seg og partikkelstørrelsen på oksidpulveret reduseres. Den ferdige homogene blandingen har konsistensen av en tykk paste. Den nøyaktige sammensetningen av ulike metalloksider og stabilisatorer bestemmer motstands-temperatur-karakteristikken og resistiviteten til de brændte keramikkomponentene.
3. Båndblanding
«Slurry» fordeler seg på en bevegelig plastbærerskive ved hjelp av doctor blade-teknologi. Den nøyaktige materialestykkelsen kontrolleres ved å justere høyden på skrapet over plastbærerskiven, farten på bærerskiven og ved å justere slurry-viskositeten. Formingsmaterialet tørres på en flat formingsbelt gjennom en lang tunnellove ved høy temperatur. Det resulterende «grønne» båndet er knekkelig og lett å forme. Deretter utføres kvalitetsinspeksjon og analyse av båndet. Termistorbåndets tykkelse varierer fra 0,001″ til 0,100″ i et bredt omfang, avhengig av spesifikke komponentspesifikasjoner.
4. Wafer-forming
Båndet er klart til å formes til plater. Når tynne materialer er nødvendige, kuttes båndet enkelt opp i små kvadrater. For tykkere plater kuttes båndet opp i kvadrater og plasseres på toppen av hverandre. Disse lagde plater lemmer man deretter sammen. Dette lar oss produsere plater med nesten den ønskte tykkelsen. Deretter går platen gjennom ytterligere kvalitetstesting for å sikre høy likformighet og kvalitet. Deretter blir platen utsatt for en binderforbrændingscyklus. Denne metoden fjerner meste av den organiske bindemidlene fra platen. For å forhindre ugunstig fysisk stress på termistorplaten, holdes nøyaktig tid/temperaturskontroll under lempingen av bindemidlet.
5. Sinter
Waferen oppvarmes til en veldig høy temperatur i en oksiderende atmosfære. Ved disse høye temperaturer reagerer oksidene med hverandre og smelter sammen for å danne en spinelkeramisk matrise. Under sinteringsprosessen tettet materialet seg til et forhåndsbestemt nivå, og korn grenser i keramikken får vokse. Hold en nøyaktig temperaturprofil under sinteringsprosessen for å unngå at waferen brytes og for å sikre produksjon av ferdige keramikkkomponenter som kan produsere deler med like elektriske egenskaper. Etter sinteringen sjekkes kvaliteten på waferen igjen, og de elektriske og fysiske egenskapene registreres.
6. Elektrode
Ohmisk kontakt med keramiske plater oppnås ved bruk av tykkfilmselektrodmateriale. Materialet er vanligvis sølv, palladiumsølv, gull eller platin, avhengig av anvendelsen. Elektrodematerialet består av en blanding av metall, glass og ulike løsemidler, og blir anvendt på de to motsatte ytene av en plade eller chip ved skjertrykking, sprøyting eller pensling. Elektrodematerialet brennes fast på keramikken i en tykkfilm-bændovn, og den elektriske koblingen og mekaniske kombinasjonen dannes mellom keramikken og elektroden. Deretter sjekkes den metalliserte platen og egenskapene registreres. Nøyaktig kontroll i elektrodeprosessen sikrer at komponentene produsert fra plater vil ha fremragende langtidstilførbarhet.
7. Terninger
Høy hastighet semiconductor skjermask er brukt til å kutte chippen i små chips. Skjermbladet bruker en diamantkant og kan produsere et stort antall ekstremt likeformige dør. Den resulterende termistorchippa kan være så liten som 0,010 “til 1000”. Størrelsen på forskjellen mellom en sett med termistorchips er faktisk umålbart. En typisk termistorchip kan produsere tusenvis av termistorchips. Etter å ha skåret, rens chippa og sjekk dimensjonene og elektriske egenskaper. Elektriske inspeksjoner inkluderer bestemmelsen av nominelle motstandsverdier for spesifikke anvendelser, motstandstemperatur karakteristikk, produksjonsutbytte, og godkjennelse av batch. Motstand og motstandstemperatur karakteristikken måles nøyaktig innenfor 0,001 ° C ved å bruke presis temperaturregulering.
8. Motstandsklassifisering
Alle termistorene testes for riktige motstandsverdier, vanligvis ved 25 °C. Disse kjernetestes vanligvis automatisk, men de kan også testes manuelt basert på produksjon og spesifikasjoner. Den automatiske kjerneprosessoren er koblet til et motstandstestelapp og en datamaskin programmert av operatøren for å plassere kjernen i ulike minneområder avhengig av dens motstandsverdi. Hver automatiske kjerneprosessor kan teste 9000 deler per time på en veldig nøyaktig måte.
9. Vedlegg av ledningstråd
I noen tilfeller selges termistorene i form av chips og krever ikke ledninger, men i de fleste tilfeller er ledninger nødvendige. Termistorchippene kobles til ledningene ved løding eller ved trykkkontakter i diodemaketten. Under løtningsprosessen plasseres termistorchippa på ledningsrammen, som avhenger av fjærspenningen i tråden for å holde chippen på plass under løtningsprosessen. Deretter druknes monteringen i en kjele med smeltet løt og trekkes opp igjen. Impregneringshastigheten og oppholdstiden kontrolleres nøyaktig for å unngå overdreven termisk støt til termistoren. Spesielle fluesmidler brukes også for å forbedre løteegenskapene uten å skade termistorchippa. Løten fastner til chippelektroner og ledninger for å gi en solid kobling mellom tråd og chip. For diodtypen “DO-35”-pakke termistor, holdes termistorchippa mellom de to ledningene på en akseal måte. En glasetsui plasseres rundt komponenten og varmes opp til høy temperatur. Glasetsua smelter rundt termistorchippa og segler til ledningen. For eksempel, i en diodstruktur, gir trykket fra glasset på modulen den nødvendige kontakten mellom ledningstråden og termistorchippa.
Ledningene som brukes for termistore er vanligvis kobber, nikkel eller legering, ofte med tin eller lodd dekning. Legeringsledningsmaterialer med lav varmeledning kan brukes i noen applikasjoner der varmetilskillelse mellom termistor og ledning kreves. I de fleste applikasjoner lar dette termistorene reagere raskere på temperaturendringer. Etter feste bør du sjekke bindingen mellom ledningen og kjernen. En sterke veldingsflate hjelper til å sikre langtidsreliabilitet av den ferdige termistoren.
10. Innkapsle
For å beskytte termistorene mot driftsatmosfære, fuktighet, kjemisk angrep og kontaktkorrosjon, dekkes ledninger på termistorer vanligvis med en beskyttende konformt coating. Læggesmålet er vanligvis epoxyresin med høy varmeledningsevne. Andre læggesmål inkluderer silicon, keramisk cement, maling, polyuretan og traksleeve. Læggesmålene bidrar også til å sikre god mekanisk integritet av utstyr. Termisk respons fra termistoren bør tas i betraktning når man velger pakkmateriale. I anvendelser der rask termisk respons er avgjørende, brukes tynne filmer av læggesmål med høy varmeledningsevne. Der miljøbeskyttelse er viktigere, kan et annet læggesmål velges. Læggesmålinger som epoxyresin, silikagel, keramisk cement, maling og polyuretan blir vanligvis behandlet ved innfrøying og hardnes på romtemperatur eller plasseres i en ovn ved økte temperaturer. Nøyaktig tid, temperatur og viskositetskontroll brukes gjennom hele prosessen for å sikre at pinhull eller andre deformasjoner ikke utvikler seg.
11. Avslutt
Termistore er vanligvis utstyrt med terminaler som er koblet til slutten av deres ledninger. Før terminalen blir montert, trekkes isolasjonen fra ledningen i den nødvendige mengden for å passe på den spesifiserte terminalen. Disse terminalene kobles til ledningene ved hjelp av en spesialmaskin for terminalanbringelse. Terminalene kan deretter settes inn i en plastisk eller metallhylle før de leveres til kunden.
12. Sømmontasje
Av miljømessige eller mekaniske årsaker er termistorene vanligvis inndukket i sonda. Disse husene kan bestå av materialer som epoxy, vinyl, rustfritt stål, aluminium, messing og plastikk. I tillegg til å gi passende mekanisk montering for termistorelementene, beskytter huset dem mot miljøet de blir utsatt for. Den riktige valget av ledninger, tråd isolering og fyllingsmaterialer vil resultere i en tilfredsstillende luting mellom termistoren og det eksterne miljøet.
13. Merknadsidentifikasjon
Den ferdige termistoren kan merkes for enkel identifisering. Dette kan være så enkelt som fargepunkter eller mer kompleks, som dato-koder og delnummer. I noen applikasjoner kan farger bli lagt til i overflatedekningen på termistor-kroppen for å oppnå en spesifikk farge. Fargepunktene legges vanligvis på termistoren ved en impregneringsprosess. Bruk en penn for å lage merker som krever alfanumeriske tegn. Denne maskinen bruker kun permanent tinte for å merke delene. Tinten fastnes ved økt temperatur.
14. Endelig Inspeksjon
Alle ferdigstilte bestillinger vil bli inspisert etter fysiske og elektriske feil på en 'null defekt'-basis. Alle parametere blir kontrollert og registrert før produktet forlater fabrikken.
15. Pakk & Send Alle termistorer og komponenter blir omhyggelig pakket og vil bli brukt av kundene.