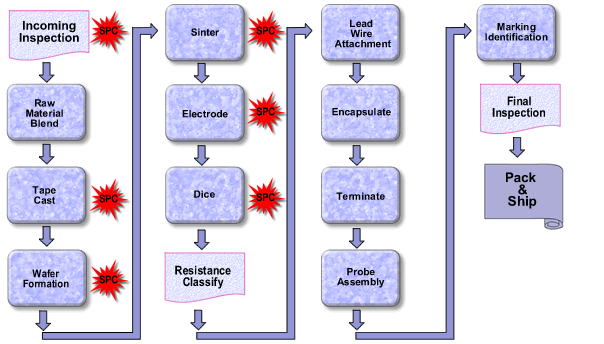
Het productieproces van NTC thermistors kan worden onderverdeeld in: Inkomende inspectie – Grondstofmengsel – Bandgieten – Wafervorming – Sinter – Elektrode – Snijden – Weerstand classificeren – Looddraadmontage – Encapsuleren – Afsluiten – Sondeassemblage – Markering en identificatie – eindinspectie – Verpakken & verzenden .
1. Inkomend controle
Alle grondstoffen worden bij ontvangst geïnspecteerd om te verifiëren of hun fysische en elektrische eigenschappen aanvaardbaar zijn. Wijs een uniek ID# toe en gebruik dit voor batch-traceerbaarheid.
2. Grondstofmengeling
De productie van NTC-thermistors begint met het nauwkeurig mengen van grondstoffen in oplossingen van organische bindmiddelen. Deze grondstoffen zijn gepulveriseerde overgangsmetaaloxiden zoals mangaan, nikkel, kobalt en koperoxide. Aan de mengsel worden ook andere stabilisatoren toegevoegd. De oxiden en binder worden gecombineerd met een nat proces dat ball milling wordt genoemd. Bij het ball milling proces worden de materialen gemengd en wordt de deeltjesgrootte van het oxidepoeder verkleind. Het eindige homogene mengsel heeft de consistentie van een dikke pasta. De exacte samenstelling van verschillende metaaloxiden en stabilisatoren bepaalt de weerstand-temperatuurkenmerken en de elektrische weerstand van de gebakken keramische componenten.
3. Tape Cast
De "slib" wordt verdeeld over een beweegbare plastic dragerplaat met behulp van doctor blade technologie. De exacte materiaaldikte wordt bepaald door aanpassing van de hoogte van de squeegee boven de plastic dragerplaat, de snelheid van de dragerplaat en door aanpassing van de viscositeit van de slib. Het gietmateriaal wordt gedroogd op een vlakke gietband door een lange tunneloven bij hoge temperatuur. Het resulterende "groene" bandje is vormbaar en gemakkelijk te formeren. Vervolgens wordt er kwaliteitscontrole en analyse uitgevoerd op de band. De dikte van de thermistorband varieert van 0,001" tot 0,100", afhankelijk van de specifieke componentenspecificaties.
4. Wafervorming
De tape is klaar om gevormd te worden tot wafers. Wanneer dunne materialen nodig zijn, snijd je de tape gewoon in kleine vierkanten. Voor dikker wafers snijdt u de tape in vierkanten en stapelt u deze op elkaar. Deze gestapelde wafers worden vervolgens gelamineerd. Dit laat ons toe wafers van bijna de vereiste dikte te produceren. Vervolgens ondergaat de wafer extra kwaliteitstesten om een hoge uniformiteit en kwaliteit te waarborgen. Daarna wordt de wafer onderworpen aan een binder verbrandingscyclus. Deze methode verwijdert de meeste organische binder uit de wafer. Om ongunstige fysieke spanningen op de thermistorwafer te voorkomen, wordt tijd/temperatuurcontrole nauwkeurig in stand gehouden gedurende de lijmpasta-verbrandingscyclus.
5. Sinteren
De wafel wordt op een zeer hoge temperatuur verwarmd in een oxidatieve atmosfeer. Bij deze hoge temperaturen reageren de oxiden met elkaar en smelten samen om een spinelkeramische matrix te vormen. Tijdens het sinterproces wordt het materiaal tot een vooraf bepaald niveau verdicht, en worden de korrelgrenzen van de keramiek toegestaan om te groeien. Houdt een nauwkeurig temperatuurprofiel aan tijdens het sinterproces om waferbreuken te voorkomen en om te zorgen voor de productie van afgeronde keramiek die onderdelen kan produceren met uniforme elektrische kenmerken. Na het sinteren wordt de kwaliteit van de wafel opnieuw geïnspecteerd en worden de elektrische en fysische kenmerken vastgelegd.
6. Elektrode
Omhische contact met keramische schijven wordt verkregen door gebruik te maken van dikke film elektrodematerialen. Het materiaal is meestal zilver, palladiumzilver, goud of platina, afhankelijk van de toepassing. Het elektrodemateriaal bestaat uit een mengsel van metaal, glas en verschillende oplosmiddelen, en wordt aangebracht op de twee tegenoverliggende oppervlakken van een schijf of chip door schermprinten, spuiten of borstelen. Het elektrodemateriaal wordt in de dikke film ceintuuroven op de keramiek gebrand, en er wordt een elektrische verbinding en mechanische combinatie gevormd tussen de keramiek en het elektrode. Vervolgens wordt de metalliseerde schijf gecontroleerd en worden de eigenschappen vastgelegd. Precieze controle in het elektrodeproces garandeert dat de componenten die zijn geproduceerd uit schijven uitstekende langdurige betrouwbaarheid zullen hebben.
7. Dobbelstenen
De hoge snelheid semiconductor snijzagen wordt gebruikt om de chip in kleine chips te verdelen. De zaagbladen gebruiken een diamantblad en kunnen een groot aantal uiterst uniforme stervormige delen produceren. De resulterende thermistor chip kan zo klein zijn als 0,010 “tot 1000”. Het verschil in chipgrootte van een setje chip thermistor chips is eigenlijk onmetelijk. Een typische thermistor chip kan duizenden thermistor chips produceren. Na het snijden, wordt de chip schoongemaakt en worden de afmetingen en elektrische kenmerken gecontroleerd. Elektrische inspecties omvatten het bepalen van nominale weerstandswaarden voor specifieke toepassingen, weerstandstemperatuurkenmerken, productieopbrengst en acceptabiliteit per partij. Weerstand en weerstandstemperatuurkenmerken worden nauwkeurig gemeten binnen 0,001 °C met behulp van precisie temperatuurbeheersing.
8. Weerstand Classificatie
Alle thermistors worden getest op de juiste weerstandswaarden, meestal bij 25 °C. Deze chips worden doorgaans automatisch getest, maar ze kunnen ook handmatig getest worden afhankelijk van de productie en specificaties. De automatische chipprocessor is verbonden met een weerstandstestapparaat en een computer die door de operator is geprogrammeerd om de chip in verschillende geheugengebieden te plaatsen afhankelijk van zijn weerstandswaarde. Elk automatische chipprocessor kan 9000 onderdelen per uur testen op een zeer nauwkeurige manier.
9. Aankoppeling Draad
In sommige gevallen worden thermistors in de vorm van chips verkocht en hebben ze geen aansluitingen nodig, maar in de meeste gevallen zijn aansluitingen vereist. De thermistorchip wordt aan de aansluitingen verbonden door te lassen of door drukcontacten in het diode-huisje. Tijdens het lasproces wordt de thermistorchip op het leadframe geladen, wat afhankelijk is van de veerkracht van het draad om de chip tijdens het lasproces vast te houden. Het geheel wordt vervolgens ondergedompeld in een pot met gesmolten lood en weer verwijderd. De impregneringsnelheid en verblijftijd worden nauwkeurig beheerd om te voorkomen dat de thermistor te veel thermische schok krijgt. Speciale fluxen worden ook gebruikt om de lasbaarheid te verbeteren zonder de thermistorchip te beschadigen. Het lood hecht zich aan de elektroden van de chip en de aansluitingen om een stevige verbinding tussen draad en chip te waarborgen. Bij het diode-type “DO-35” thermistorhuisje wordt de thermistorchip axiaal tussen de twee aansluitingen gehouden. Een glazen huls wordt rond het component geplaatst en op hoge temperatuur verhit. De glazen huls smelt rond de thermistorchip en wordt aan het aansluitdraad vastgemaakt. Bijvoorbeeld, in een diodestructuur biedt de druk van het glas op het module de noodzakelijke contacten tussen het aansluitdraad en de thermistorchip.
De aansluitingen die worden gebruikt voor thermistors zijn meestal koper, nikkel of legering, vaak met een tin- of soldercoating. In sommige toepassingen kunnen legeringen met een lage thermische geleiheid als geleidersmateriaal worden gebruikt waar thermische isolatie tussen thermistor en geleider vereist is. In de meeste toepassingen laat dit thermistors sneller reageren op temperatuurveranderingen. Na het bevestigen, controleer je de verbinding tussen de aansluiting en de chip. Een sterke weldinterface zorgt ervoor dat de betrouwbaarheid van de voltooide thermistor op lange termijn wordt gegarandeerd.
10. Encapsuleren
Om thermistors te beschermen tegen de werkingsatmosfeer, vochtigheid, chemische aanvallen en corrosie door contact, worden thermistors met leads doorgaans voorzien van een beschermende conformal coating. De afsluitmiddelen zijn meestal epoxyharsen met hoge warmtegeleiding. Andere afsluitmiddelen omvatten silicones, keramische cementen, verf, polyurethane en krimpfolie. Afsluitmiddelen helpen ook om de mechanische integriteit van het apparaat te waarborgen. De thermische respons van de thermistor moet in aanmerking worden genomen bij het kiezen van verpakkingsmaterialen. In toepassingen waarbij een snelle thermische respons cruciaal is, worden dunne lagen van afsluitmiddelen met hoge warmtegeleiding gebruikt. Wanneer milieubescherming belangrijker is, kan een ander afsluitmiddel worden geselecteerd. Afsluitmiddelen zoals epoxyharst, silicagel, keramische cementen, verf en polyurethane worden doorgaans aangebracht door impregneren en op kamertemperatuur of in een oven op verhoogde temperaturen gehard. Tijdens het proces wordt nauwkeurig gecontroleerd op tijd, temperatuur en viscositeit om te zorgen dat geen poriën of andere deformiteiten ontstaan.
11. Afsluiten
Thermistors zijn meestal uitgerust met terminalen die zijn verbonden met het einde van hun aansluitdraden. Voordat de terminal wordt aangebracht, wordt de isolatie van de draad correct weggestript om te passen bij de gespecificeerde terminal. Deze terminalen worden met een speciale tool applicatie machine aan de draden gekoppeld. De terminalen kunnen daarna in een kunststof- of metaalgehuisvest worden geplaatst voordat ze worden afgeleverd aan de klant.
12. Sonda montage
Voor milieubescherming of mechanische redenen worden thermistors doorgaans in de sondehuls geplaatst. Deze huizen kunnen bestaan uit materialen zoals epoxy, vinyl, roestvrij staal, aluminium, koper en kunststof. Naast het verschaffen van een geschikte mechanische bevestiging voor de thermistorelementen, beschermt de huls ze tegen de omgeving waar ze aan blootgesteld zijn. De juiste keuze van leidingsmaterialen, draadisolatie en afgietsmateriaal zorgt voor een tevredenstellende afsluiting tussen de thermistor en de externe omgeving.
13. Markering Identificatie
De afgeronde thermistor kan worden gemarkeerd voor eenvoudige identificatie. Dit kan zo eenvoudig zijn als kleurstippen of complexer, zoals datumcodes en onderdelennummers. In sommige toepassingen kunnen kleurstoffen worden toegevoegd aan de coating op het thermistorlichaam om een specifieke kleur te verkrijgen. De kleurstippen worden meestal toegevoegd aan de thermistor door een doordringingsproces. Gebruik een pen om labels te genereren die alfanumerieke tekens vereisen. Deze machine gebruikt alleen permanente inkt om onderdelen te markeren. De inkt verstevigt bij verhoogde temperatuur.
14. Eindcontrole
Alle voltooide orders worden geïnspecteerd op fysieke en elektrische gebreken op basis van 'nul gebreken'. Alle parameters worden gecontroleerd en vastgelegd voordat het product de fabriek verlaat.
15. Verpakken & Vervoeren Alle thermistors en onderdelen worden zorgvuldig verpakt en zullen worden gebruikt door klanten.