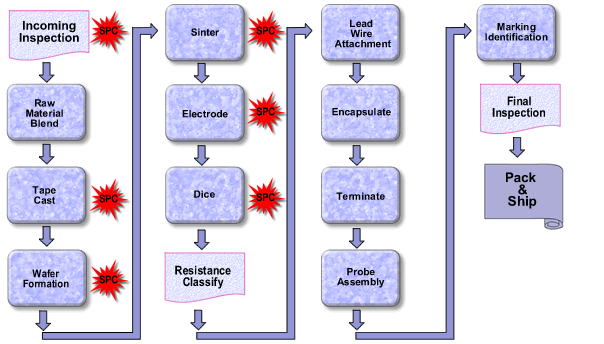
Proses pembuatan termistor NTC boleh dibahagikan kepada: Pemeriksaan Masukan – Campuran Bahan Mentah – Pengecasan Lembaran – Pembentukan Wafer – Sinter – Elektrod – Dadah – Klasifikasi Rintangan – Pengikatan Dawai Penyulit – Kapsul – Penamat – Perakitan Sonda – Penandaan Pengenalan – pemeriksaan akhir – Bungkus & Hantar .
1. Pemeriksaan Masuk
Semua bahan mentah diperiksa semasa diterima untuk memastikan sama ada sifat fizik dan elektrik mereka adalah dapat diterima. Tetapkan ID# unik dan gunakannya untuk pelacakkan batc.
2. Campuran Bahan Mentah
Pembuatan termoduktor NTC bermula dengan pencampuran tepat bahan mentah ke dalam larutan pengikat organik. Bahan mentah ini termasuk oksida logam transisi berbentuk serbuk seperti mangan, nikel, kobalt dan oksida tembaga. Pemantap lain juga ditambahkan ke dalam campuran tersebut. Oksida dan pengikat dicampur menggunakan teknik proses basah yang dipanggil ball milling. Dalam proses ball milling, bahan-bahan itu dicampur dan saiz zarah serbuk oksida dikurangkan. Campuran homogen akhir mempunyai konsistensi seperti pasta tebal. Komposisi tepat pelbagai oksida logam dan pemantap menentukan ciri-ciri rintangan-suhu dan rintangan komponen keramik yang ditempa.
3. Penyusunan Lembaran
‘Slurry’ dipanaskan di atas lembaran pembawa plastik yang bergerak dengan menggunakan teknologi bilah doktor. Ketebalan bahan dikawal dengan tepat dengan menyesuaikan ketinggian penyapu di atas lembaran pembawa plastik, laju lembaran pembawa dan dengan menyesuaikan kekentalan slurry. Bahan pengecasan dikeringkan pada belt pengecasan rata melalui oven terowong panjang pada suhu tinggi. ‘Green’ tape yang dihasilkan adalah mudah dibentuk dan fleksibel. Kemudian, lakukan pemeriksaan kualiti dan analisis pada tape. Ketebalan tape termistor berkisar antara 0.001″ hingga 0.100″ dalam julat luas, bergantung kepada spesifikasi komponen tertentu.
4. Pembentukan Wafer
Pita sudah siap untuk dibentuk menjadi wafer. Apabila bahan nipis diperlukan, hanya memotong pita ke dalam kotak kecil. Untuk wafer yang lebih tebal, potong pita ke dalam segi empat dan tumpukan di atas yang lain. Wafer yang ditumpuk ini kemudian dilaminasi bersama. Ini membolehkan kami menghasilkan wafer hampir ketebalan yang diperlukan. Kemudian, wafer menjalani ujian kualiti tambahan untuk memastikan keseragaman dan kualiti yang tinggi. Kemudian, wafer ini dikenakan kitaran kehabisan pengikat. Kaedah ini mengeluarkan sebahagian besar pengikat organik dari wafer. Untuk mengelakkan tekanan fizikal yang buruk pada wafer termistor, kawalan masa/suhu yang tepat dikekalkan semasa kitaran pembakaran pelekat.
5. Penyinteran
Wafer dipanaskan kepada suhu yang sangat tinggi dalam atmosfera pengoksidaan. Pada suhu tinggi ini, oksida-oksida bertindak balas dengan satu sama lain dan bergabung untuk membentuk matriks keramik spinel. Semasa proses sinting, bahan itu diperkatkan kepada tahap yang telah ditetapkan, dan sempadan bijirin keramik dibenarkan tumbuh. Kekalkan profil suhu yang tepat semasa proses sinting untuk mengelakkan pecahnya wafer dan memastikan pengeluaran keramik jadi yang boleh menghasilkan bahagian dengan ciri-ciri elektrik yang seragam. Selepas sinting, kualiti wafer diperiksa sekali lagi, dan ciri-ciri elektrik dan fizikal dicatat.
6. Elektrod
Kontak ohm dengan keping keramik diperoleh menggunakan bahan elektrod tebal. Bahan tersebut biasanya adalah perak, paduk perak, emas atau platinum, bergantung kepada aplikasi. Bahan elektrod terdiri daripada campuran logam, kaca dan pelbagai penyelesa, dan diterapkan pada dua permukaan bertentangan sebuah keping atau cip melalui pencetakan skrin, penyembur atau pensatan. Bahan elektrod dipanggang pada keramik dalam ketuhar pita tebal, dan persatuan elektrik serta mekanikal terbentuk di antara keramik dan elektrod. Kemudian semak keping yang telah dimetalisasi dan rekodkan sifat-sifatnya. Kawalan tepat dalam proses elektrod memastikan komponen yang dihasilkan daripada keping akan mempunyai kebolehpercayaan jangka panjang yang cemerlang.
7. Dadu
Penggera semikonduktor berkelajuan tinggi digunakan untuk memotong cip menjadi cip kecil. Mata pisaunya menggunakan mata berlian dan boleh menghasilkan bilangan besar cip yang sangat seragam. Cip termistor yang dihasilkan boleh serendah 0.010 “hingga 1000”. Beza saiz cip dalam satu set cip termistor sebenarnya adalah tidak dapat diukur. Sebuah cip termistor tipikal boleh menghasilkan ribuan cip termistor. Selepas dipotong, cip itu dibersihkan dan dimaklumkan dengan dimensi serta ciri-ciri elektrik. Pemeriksaan elektrik termasuk penentuan nilai rintangan nominal untuk aplikasi spesifik, ciri-ciri suhu rintangan, hasil pengeluaran, dan keterterimaan batch. Rintangan dan ciri-ciri suhu rintangan diukur dengan tepat dalam julat 0.001 ° C menggunakan kawalan suhu yang tepat.
8. Klasifikasi Rintangan
Semua termistor diuji untuk nilai rintangan yang betul, biasanya 25 ° C. Cip ini biasanya diuji secara automatik, tetapi mereka juga boleh diuji secara manual berdasarkan pengeluaran dan spesifikasi. Pemproses cip automatik disambungkan ke peranti ujian rintangan dan komputer yang diprogram oleh pengendali untuk meletakkan cip di pelbagai kawasan memori bergantung pada nilai rintangnya. Setiap pemproses cip automatik boleh menguji 9000 bahagian sejam dengan cara yang sangat tepat.
9. Penyambungan Dawai
Dalam beberapa kes, termistor dijual dalam bentuk cip dan tidak memerlukan pautan, tetapi dalam kebanyakan kes, pautan adalah diperlukan. Cip termistor disambungkan kepada pautan melalui penyolderan atau melalui titik tekanan dalam bungkusan diod. Semasa proses penyambungan, cip termistor dipasang pada rangka pautan, yang bergantung kepada tegangan spring kawat untuk mengekalkan cip semasa proses penyambungan. Kemudian, perakitan itu dicelupkan ke dalam periuk solder lebur dan dikeluarkan. Kadar penetrasi dan masa kediaman dikawal dengan tepat untuk mengelakkan teruja terma berlebihan kepada termistor. Flux istimewa juga digunakan untuk meningkatkan kebolehansolderan tanpa merosakkan cip termistor. Solder melekat pada elektrod cip dan pautan untuk memberikan ikatan kukuh antara kawat dan cip. Bagi bungkusan jenis diod “DO-35” termistor, cip termistor dipertahankan di antara dua pautan secara aksial. Selubung kaca diletakkan di sekeliling komponen dan dipanaskan hingga suhu tinggi. Selubung kaca melebur di sekitar cip termistor dan disegel kepada pautan. Sebagai contoh, dalam struktur diod, tekanan yang diberi oleh kaca pada modul menyediakan titik kontak yang diperlukan antara kawat pautan dan cip termistor.
Kabel yang digunakan untuk termistor biasanya terbuat dari tembaga, nikel atau loyak, biasanya dilapisi dengan timah atau timah. Bahan konduktor liga dengan kekonduksian termal rendah boleh digunakan dalam beberapa aplikasi di mana pemisahan termal antara termistor dan konduktor diperlukan. Dalam kebanyakan aplikasi, ini membolehkan termistor untuk merespon kepada perubahan suhu dengan lebih cepat. Selepas pemasangan, semak ikatan antara kabel dan cip. Antara muka penyambungan yang kuat membantu memastikan kebolehpercayaan jangka panjang termistor yang selesai.
10. Kapsul
Untuk melindungi termistor dari atmosfera operasi, kelembapan, serangan kimia dan kakisan sentuhan, termistor plumbum biasanya dilapisi dengan salutan perlindungan yang sesuai. Pelupusan biasanya resin epoksi dengan konduktiviti haba yang tinggi. Pelupusan lain termasuk silikon, simen seramik, cat, poliuretan dan lengan mengecil. Pelupusan juga membantu memastikan integriti mekanikal peralatan yang baik. Tindak balas haba termistor harus dipertimbangkan semasa memilih bahan pembungkusan. Dalam aplikasi di mana tindak balas haba yang cepat adalah kritikal, filem penyegelan konduktiviti haba yang tinggi digunakan. Di mana perlindungan alam sekitar lebih penting, pelupusan lain boleh dipilih. Pelupusan seperti resin epoksi, silika gel, simen seramik, cat, dan poliuretan biasanya dilapisi dengan impregnasi dan dikeras pada suhu bilik atau diletakkan di dalam ketuhar pada suhu tinggi. Waktu yang tepat, kawalan suhu dan kelikatan digunakan sepanjang proses untuk memastikan bahawa lubang pin atau kecacatan lain tidak berkembang.
11. Penghentian
Termistor biasanya dilengkapi dengan terminal yang disambungkan ke hujung kabel mereka. Sebelum terminal digunakan, penebat pada wayar plumbum dikeluarkan dengan betul untuk sesuai dengan terminal yang ditentukan. Terminal ini disambungkan ke wayar menggunakan mesin aplikasi alat khas. Terminal kemudian boleh dimasukkan ke dalam kandang plastik atau logam sebelum dihantar kepada pelanggan.
12. Perakitan Penyondar
Untuk tujuan perlindungan alam sekitar atau mekanikal, termistor biasanya direndam dalam kes probe. Kotak-kotak ini boleh dibuat daripada bahan-bahan termasuk epoksi, vinil, keluli tahan karat, aluminium, kuningan dan plastik. Selain menyediakan pemasangan mekanikal yang sesuai untuk elemen termistor, kotak ini melindungi mereka dari persekitaran yang mereka terpapar kepada. Pemilihan yang betul bagi wayar, penyelubung wayar dan bahan potting akan menghasilkan segel yang memuaskan di antara termistor dan persekitaran luar.
13. Penandaan Pengenalan
Termostat yang selesai boleh ditanda untuk pengenalan yang mudah. Ini boleh serupa dengan titik warna yang mudah atau lebih kompleks, seperti kod tarikh dan nombor bahagian. Dalam beberapa aplikasi, pewarna boleh ditambahkan kepada pelapisan di atas badan termostat untuk mendapatkan warna tertentu. Titik warna biasanya ditambahkan kepada termostat melalui proses imbasan. Gunakan penanda untuk menghasilkan tag yang memerlukan aksara alfanumerik. Mesin ini hanya menggunakan tinta kekal untuk menanda bahagian. Tinta itu mengeras pada suhu tinggi.
14. Pemeriksaan Akhir
Semua pesanan yang selesai akan diperiksa untuk kecacatan fizikal dan elektrik berdasarkan asas 'tiada cacat'. Semua parameter diperiksa dan direkodkan sebelum produk meninggalkan kilang.
15. Bungkus & Hantar Semua termostat dan komponen dibungkus dengan teliti dan akan digunakan oleh pelanggan.