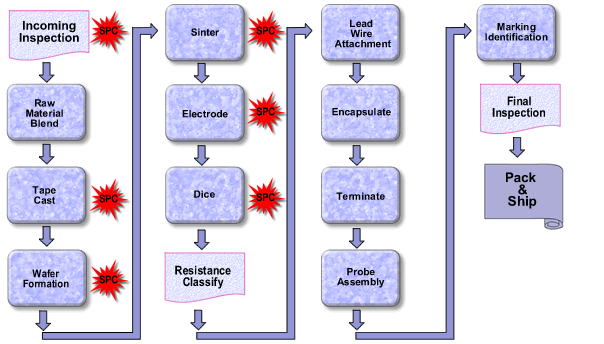
Il processo di produzione del termistor NTC può essere diviso in: Ispezione in Arrivo – Impasto dei Materiali Grezzi – Formatura a Nastro – Formazione della Wafer – Sinterizzare – Elettrodo – Dado – Classificazione della Resistenza – Fixaggio del Filo di Collegamento – Incapsulamento – Terminazione – Assemblaggio delle Sonde – Identificazione con Marchiatura – ispezione finale – Imballaggio e Spedizione .
1. Ispezione in Arrivo
Tutti i materiali grezzi vengono ispezionati al momento della ricevuta per verificare se le loro proprietà fisiche ed elettriche sono accettabili. Viene assegnato un ID# unico e utilizzato per la tracciabilità del lotto.
2. Miscela di Materie Prime
La produzione di termistori NTC inizia con il miscelamento preciso delle materie prime in soluzioni di legante organico. Queste materie prime sono ossidi metallici in polvere come manganese, nichel, cobalto e ossido di rame. Vengono anche aggiunti altri stabilizzatori alla miscela. L'ossido e il legante vengono combinati utilizzando una tecnica chiamata macinazione a palline. Nel processo di macinazione a palline, le materie vengono mescolate e la dimensione delle particelle della polvere d'ossido viene ridotta. La miscela omogenea finale ha la consistenza di una pasta spessa. La composizione esatta di vari ossidi metallici e stabilizzatori determina le caratteristiche resistenza-temperatura e la resistività dei componenti ceramici dopo la cottura.
3. Formatura a Nastro
La “pasta” viene distribuita su una lamiera plastica mobile utilizzando la tecnologia del righello dottore. Lo spessore esatto del materiale viene controllato regolando l'altezza della spatola sopra la lamiera plastica, la velocità della lamiera e regolando la viscosità della pasta. Il materiale da fondere viene asciugato su una cinghia piatta attraverso un forno tunnel a lunga temperatura elevata. Il nastro risultante è malleabile e facile da formare. Successivamente vengono eseguite ispezioni e analisi di qualità sul nastro. Lo spessore del nastro termistor varia da 0,001" a 0,100" in un ampio intervallo, a seconda delle specifiche del componente specifico.
4. Formazione della wafer
La nastro è pronto per essere formato in wafer. Quando sono necessari materiali sottili, basta tagliare il nastro in piccoli quadrati. Per wafer più spessi, tagliare il nastro in quadrati e sovrapporli. Questi wafer sovrapposti vengono poi laminati insieme. Ciò ci consente di produrre wafer quasi della spessore richiesto. Successivamente, il wafer subisce ulteriori test di qualità per garantire una alta uniformità e qualità. Successivamente, il wafer viene sottoposto a un ciclo di eliminazione del legante. Questo metodo rimuove la maggior parte del legante organico dal wafer. Al fine di prevenire stress fisici indesiderati sul wafer del termistor, durante il ciclo di bruciatura del legante viene mantenuto un controllo preciso del tempo/temperatura.
5. Frittura
La wafer viene riscaldata a una temperatura molto alta in un'atmosfera ossidante. A queste alte temperature, gli ossidi reagiscono tra loro e si fondono insieme per formare una matrice ceramica spinello. Durante il processo di sintetizzazione, il materiale viene reso compatto fino a un livello prestabilito, e vengono consentite la crescita dei confini di grano della ceramica. Si mantenga un profilo di temperatura preciso durante il processo di sintetizzazione per evitare fratture della wafer e garantire la produzione di ceramiche finite che possono produrre componenti con caratteristiche elettriche uniformi. Dopo la sintetizzazione, viene effettuata nuovamente un'ispezione sulla qualità della wafer e vengono registrate le caratteristiche elettriche e fisiche.
6. Elettrodo
Il contatto ohmico con i wafer ceramici viene ottenuto utilizzando materiali per elettrodi a spessa film. Il materiale è solitamente argento, palladio-argento, oro o platino, a seconda dell'applicazione. L'elettrodo è composto da un miscuglio di metallo, vetro e vari solventi, e viene applicato sulle due superfici opposte di un wafer o chip tramite stampa a schermo, spruzzatura o pennellatura. L'elettrodo viene fissato sulla ceramica nel forno a nastro per spessa film, e si forma la giunzione elettrica e la combinazione meccanica tra la ceramica e l'elettrodo. Successivamente, si verifica il wafer metallizzato e si registrano le sue proprietà. Un controllo preciso nel processo di elettrodo garantisce che i componenti prodotti dai wafer abbiano un'eccellente affidabilità a lungo termine.
7. Dadi
La sega ad alta velocità per semiconduttori viene utilizzata per tagliare il chip in piccoli chip. La lama della sega utilizza una lama in diamante e può produrre un gran numero di dadi estremamente uniformi. Il termistor risultante può essere piccolo come 0,010 “fino a 1000”. La differenza di dimensioni tra un gruppo di chip termistor è effettivamente immisurabile. Un tipico chip termistor può produrre migliaia di chip termistor. Dopo il taglio, si pulisce il chip e si controllano le dimensioni e le caratteristiche elettriche. I controlli elettrici includono la determinazione dei valori di resistenza nominali per applicazioni specifiche, delle caratteristiche di resistenza-temperatura, del tasso di produzione e dell'accettabilità del lotto. Resistenza e caratteristiche di resistenza-temperatura vengono misurate con precisione entro 0,001 °C utilizzando un controllo preciso della temperatura.
8. Classificazione della Resistenza
Tutti i termistori vengono testati per verificare i valori di resistenza corretti, di solito a 25 °C. Questi chip vengono generalmente testati in modo automatico, ma possono anche essere testati manualmente in base alla produzione e alle specifiche. Il processore automatico dei chip è collegato a un dispositivo di test di resistenza e a un computer programmato dall'operatore per posizionare il chip in diverse aree di memoria in base al suo valore di resistenza. Ogni processore automatico di chip può testare 9000 parti all'ora in modo molto preciso.
9. Attaccatura del Filo
In alcuni casi, i termistori vengono venduti sotto forma di chip e non richiedono terminali, ma nella maggior parte dei casi sono necessari i fili. Il chip del termistore viene collegato ai fili mediante saldatura o tramite contatti a pressione nel pacchetto del diodo. Durante il processo di saldatura, il chip del termistore viene posizionato sul telaio dei fili, che si basa sulla tensione elastica del filo per mantenere il chip durante la saldatura. L'assemblaggio viene quindi immerso in una pentola con saldatura fusa e rimosso. La velocità di imbibizione e il tempo di permanenza sono controllati con precisione per evitare uno shock termico eccessivo al termistore. Vengono utilizzate anche speciali pastiglie per migliorare la saldabilità senza danneggiare il chip del termistore. La saldatura aderisce agli elettrodi del chip e ai fili per fornire un solido legame tra filo e chip. Per il termistore con pacchetto di tipo “DO-35” a diodo, il chip del termistore viene mantenuto tra i due fili in modo assiale. La manica di vetro viene posta intorno al componente e riscaldata a alta temperatura. La manica di vetro si fonde intorno al chip del termistore e viene sigillata al filo. Ad esempio, in una struttura a diodo, la pressione esercitata dal vetro sul modulo fornisce il contatto necessario tra il filo e il chip del termistore.
I fili utilizzati per i termistori sono solitamente in rame, nichel o lega, spesso con rivestimento in stagno o saldaturo. In alcune applicazioni possono essere utilizzati materiali conduttori a bassa conducibilità termica quando è richiesta una isolazione termica tra il termistore e il conduttore. In gran parte delle applicazioni, ciò consente ai termistori di reagire più rapidamente ai cambiamenti di temperatura. Dopo l'attaccatura, controllare la saldatura tra il filo e il chip. Un'interfaccia di saldatura robusta aiuta a garantire la affidabilità a lungo termine del termistore completato.
10. Incapsulare
Per proteggere i termistori dall'atmosfera di funzionamento, umidità, attacco chimico e corrosione per contatto, i termistori a filo vengono generalmente rivestiti con un rivestimento protettivo conformale. Il sigillante è solitamente una resina epoxide ad alta conducibilità termica. Altri sigillanti includono silicone, cemento ceramico, vernice, poliuretano e maniche termo-restringenti. I sigillanti aiutano anche a garantire una buona integrità meccanica dell'attrezzatura. La risposta termica del termistore deve essere presa in considerazione quando si sceglie il materiale di imballaggio. In applicazioni in cui la risposta termica rapida è critica, vengono utilizzati strati di sigillanti ad alta conducibilità termica. Dove la protezione ambientale è più importante, può essere selezionato un altro sigillante. Sigillanti come resina epoxide, silicone, cemento ceramico, vernice e poliuretano vengono generalmente applicati per impregnazione e curati a temperatura ambiente o posti in un forno a temperature elevate. Un controllo preciso del tempo, della temperatura e della viscosità viene utilizzato durante tutto il processo per garantire che non si sviluppino pori o altre deformità.
11. Terminare
I termistors sono generalmente dotati di terminali connessi alle estremità dei loro fili. Prima dell'applicazione del terminale, l'isolamento del filo viene opportunamente rimossa per adattarsi al terminale specificato. Questi terminali vengono connessi ai fili utilizzando una macchina applicatrice speciale. I terminali possono poi essere inseriti in un involucro di plastica o metallo prima di essere consegnati al cliente.
12. Assemblaggio della sonda
Per motivi di protezione ambientale o meccanici, i termistori vengono generalmente immersi nel caso della sonda. Queste custodie possono essere realizzate in materiali tra cui epossidico, vinile, acciaio inox, alluminio, rame e plastica. Oltre a fornire un adeguato supporto meccanico per gli elementi termistors, la custodia li protegge dall'ambiente a cui sono esposti. La corretta selezione dei materiali per i fili, l'isolamento del cavo e il materiale di riempimento garantirà un sigillo soddisfacente tra il termistore e l'ambiente esterno.
13. Identificazione della Marcatura
Il termistore finito può essere contrassegnato per un facile riconoscimento. Questo può essere semplice come punti colorati o più complesso, come codici data e numeri di parte. In alcune applicazioni, possono essere aggiunti coloranti al rivestimento del corpo del termistore per ottenere un colore specifico. I punti colorati vengono solitamente aggiunti al termistore tramite un processo di imbevimento. Usare un pennarello per generare etichette che richiedono caratteri alfanumerici. Questa macchina utilizza solo inchiostro permanente per contrassegnare le parti. L'inchiostro si solidifica a temperatura elevata.
14. Ispezione Finale
Tutti gli ordini completati verranno ispezionati per difetti fisici ed elettrici su una base di 'zero difetti'. Tutti i parametri vengono controllati e registrati prima che il prodotto lasci la fabbrica.
15. Imballaggio e Spedizione Tutti i termistori e componenti vengono imballati con cura e saranno utilizzati dai clienti.