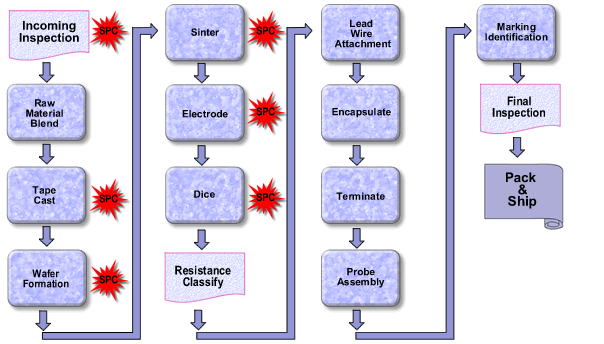
Proses manufaktur termistor NTC dapat dibagi menjadi: Pemeriksaan Masuk – Campuran Bahan Baku – Pencetakan Pita – Pembentukan Wafer – Sinter – Elektroda – Dadu – Klasifikasi Resistensi – Pemasangan Kabel Pengarah – Enkapsulasi – Menghentikan – Perakitan Probe – Identifikasi Tanda – Inspeksi akhir – Bungkus & Kirim .
1. Pemeriksaan Masuk
Semua bahan baku diperiksa saat diterima untuk memverifikasi apakah sifat fisik dan listriknya dapat diterima. Tetapkan ID# unik dan gunakan untuk pelacakan batch.
2. Campuran Bahan Baku
Pembuatan termistor NTC dimulai dengan pencampuran bahan baku secara presisi ke dalam larutan pengikat organik. Bahan baku ini berupa oksida logam transisi bubuk seperti mangan, nikel, kobalt, dan oksida tembaga. Stabilisator lainnya juga ditambahkan ke dalam campuran tersebut. Oksida dan pengikat dicampur menggunakan teknik proses basah yang disebut ball milling. Dalam proses ball milling, bahan-bahan tersebut dicampur dan ukuran partikel bubuk oksida dikurangi. Campuran homogen yang selesai memiliki konsistensi seperti pasta tebal. Komposisi tepat dari berbagai oksida logam dan stabilisator menentukan karakteristik resistansi-suhu dan resistivitas komponen keramik yang dipanggang.
3. Pencetakan Lembaran
Slurry" didistribusikan pada lembaran pembawa plastik yang bergerak menggunakan teknologi doctor blade. Ketebalan material yang tepat dikontrol dengan menyesuaikan ketinggian squeegee di atas lembaran pembawa plastik, kecepatan lembaran pembawa, dan dengan menyesuaikan viskositas slurry. Material pengecoran dikeringkan pada sabuk pengecoran datar melalui oven terowongan panjang pada suhu tinggi. Hasilnya adalah "green" tape yang lentur dan mudah dibentuk. Kemudian dilakukan pemeriksaan kualitas dan analisis pada tape. Ketebalan tape termistor berkisar dari 0,001" hingga 0,100" dalam rentang yang luas, tergantung pada spesifikasi komponen tertentu.
4. Pembentukan Wafer
Pita siap untuk dibentuk menjadi wafer. Ketika material tipis diperlukan, cukup potong pita menjadi kotak-kotak kecil. Untuk wafer yang lebih tebal, potong pita menjadi kotak dan tumpuk di atas yang lain. Wafer-wafer yang ditumpuk ini kemudian dilaminasi bersama. Ini memungkinkan kita menghasilkan wafer dengan ketebalan hampir sesuai yang diinginkan. Kemudian, wafer menjalani pengujian kualitas tambahan untuk memastikan keseragaman dan kualitas tinggi. Selanjutnya, wafer mengalami siklus pembakaran perekat. Metode ini menghilangkan sebagian besar perekat organik dari wafer. Untuk mencegah stres fisik yang merugikan pada wafer termistor, kontrol waktu/suhu yang tepat dipertahankan selama siklus pembakaran perekat.
5. Sinter
Wafer dipanaskan hingga suhu sangat tinggi dalam atmosfer oksidatif. Pada suhu tinggi ini, oksida-oksida bereaksi satu sama lain dan bergabung untuk membentuk matriks keramik spinel. Selama proses sintesis, material dikompakskan hingga tingkat yang telah ditentukan, dan batas butir keramik diizinkan tumbuh. Pertahankan profil suhu yang tepat selama proses sintesis untuk menghindari pecahnya wafer dan memastikan produksi keramik jadi yang dapat menghasilkan komponen dengan karakteristik listrik yang seragam. Setelah sintesis, kualitas wafer diperiksa lagi, dan karakteristik listrik serta fisik dicatat.
6. Elektroda
Kontak ohmik dengan wafer keramik diperoleh menggunakan bahan elektroda film tebal. Bahan tersebut biasanya perak, palladium perak, emas atau platinum, tergantung pada aplikasinya. Bahan elektroda terdiri dari campuran logam, kaca, dan berbagai pelarut, dan diterapkan pada dua permukaan berlawanan sebuah wafer atau chip melalui pencetakan layar, penyemprotan atau penggosokan. Bahan elektroda dipanggang pada keramik di tungku sabuk film tebal, dan sambungan listrik serta kombinasi mekanis terbentuk antara keramik dan elektroda. Kemudian periksa wafer yang telah dimetalisasi dan catat sifat-sifatnya. Pengendalian yang tepat dalam proses elektroda memastikan bahwa komponen yang dihasilkan dari wafer akan memiliki keandalan jangka panjang yang sangat baik
7. Dadu
Penggerinda semi konduktor berkecepatan tinggi digunakan untuk memotong chip menjadi chip kecil. Mata pisaunya menggunakan mata berlian dan dapat menghasilkan jumlah besar die yang sangat seragam. Chip termistor hasilnya bisa sekecil 0,010 “hingga 1000”. Perbedaan ukuran chip dari satu set chip termistor hampir tidak terukur. Chip termistor tipikal dapat menghasilkan ribuan chip termistor. Setelah pemotongan, bersihkan chip dan periksa dimensi serta karakteristik listriknya. Pemeriksaan listrik mencakup penentuan nilai hambatan nominal untuk aplikasi tertentu, karakteristik suhu hambatan, hasil produksi, dan keterimaan batch. Hambatan dan karakteristik hambatan suhu diukur dengan akurat dalam rentang 0,001 °C menggunakan kontrol suhu presisi.
8. Klasifikasi Hambatan
Semua termistor diuji untuk nilai resistansi yang tepat, biasanya pada 25 °C. Chip-chip ini biasanya diuji secara otomatis, tetapi juga dapat diuji secara manual berdasarkan produksi dan spesifikasi. Prosesor chip otomatis terhubung ke perangkat uji resistansi dan komputer yang diprogram oleh operator untuk menempatkan chip ke berbagai area memori bergantung pada nilai resistansinya. Setiap prosesor chip otomatis dapat menguji 9000 bagian per jam dengan cara yang sangat akurat.
9. Pemasangan Kabel Penghubung
Dalam beberapa kasus, termistor dijual dalam bentuk chip dan tidak memerlukan kawat, tetapi dalam sebagian besar kasus kawat diperlukan. Chip termistor dihubungkan ke kawat dengan penyolderan atau melalui kontak tekanan dalam paket dioda. Selama proses penyambungan, chip termistor dipasang pada rangka kawat, yang bergantung pada tegangan pegas kawat untuk menjaga chip selama proses penyambungan. Kemudian, perakitan tersebut dicelupkan ke dalam panci timah cair dan diangkat. Tingkat impregnasi dan waktu tinggal dikontrol secara presisi untuk menghindari goncangan termal berlebihan pada termistor. Flux khusus juga digunakan untuk meningkatkan kemampuan penyolderan tanpa merusak chip termistor. Timah menempel pada elektroda chip dan kawat untuk memberikan ikatan kuat antara kawat dan chip. Untuk paket termistor tipe dioda “DO-35”, chip termistor diletakkan di antara dua kawat secara aksial. Selubung kaca ditempatkan di sekitar komponen dan dipanaskan hingga suhu tinggi. Selubung kaca meleleh di sekitar chip termistor dan disegel ke kawat. Sebagai contoh, dalam struktur dioda, tekanan yang diberikan oleh kaca pada modul menyediakan kontak yang diperlukan antara kawat dan chip termistor.
Kawat yang digunakan untuk termistor biasanya terbuat dari tembaga, nikel atau paduan, biasanya dilapisi timah atau solder. Bahan konduktor paduan dengan konduktivitas termal rendah dapat digunakan dalam beberapa aplikasi di mana isolasi termal antara termistor dan konduktor diperlukan. Pada sebagian besar aplikasi, ini memungkinkan termistor merespons perubahan suhu lebih cepat. Setelah pemasangan, periksa ikatan antara kawat dan chip. Antarmuka penyambungan yang kuat membantu memastikan keandalan jangka panjang termistor yang selesai.
10. Enkapsulasi
Untuk melindungi termistor dari atmosfer operasi, kelembapan, serangan kimia, dan korosi kontak, termistor biasanya dilapisi dengan lapisan pelindung yang sesuai. Sealant umumnya adalah resin epoksi dengan konduktivitas termal tinggi. Sealant lainnya meliputi silikon, semen keramik, cat, poliuretan, dan selubung penyusut. Sealant juga membantu memastikan integritas mekanis yang baik dari peralatan. Respon termal termistor harus dipertimbangkan saat memilih bahan kemasan. Dalam aplikasi di mana respon termal cepat sangat kritis, film sealant dengan konduktivitas termal tinggi digunakan. Di mana perlindungan lingkungan lebih penting, sealant lain dapat dipilih. Sealant seperti resin epoksi, gel silika, semen keramik, cat, dan poliuretan biasanya dilapisi melalui proses imersi dan dikeringkan pada suhu ruangan atau ditempatkan di oven pada suhu tinggi. Pengendalian waktu, suhu, dan viskositas yang tepat digunakan sepanjang proses untuk memastikan bahwa pori-pori atau deformitas lain tidak terbentuk.
11. Terminasi
Termistor biasanya dilengkapi dengan terminal yang terhubung ke ujung kawatnya. Sebelum terminal dipasang, isolasi pada kawat telah dikupas dengan benar agar sesuai dengan terminal yang ditentukan. Terminal-terminal ini dihubungkan ke kawat menggunakan mesin aplikasi alat khusus. Terminal kemudian dapat dimasukkan ke dalam penyimpanan plastik atau logam sebelum dikirimkan kepada pelanggan.
12. Perakitan Probe
Untuk perlindungan lingkungan atau tujuan mekanis, termistor biasanya direndam dalam kasus probe. Penutup ini dapat terbuat dari bahan-bahan seperti epoksi, vinil, baja tahan karat, aluminium, kuningan, dan plastik. Selain memberikan pemasangan mekanis yang sesuai untuk elemen termistor, penutup tersebut melindungi mereka dari lingkungan yang mereka hadapi. Pemilihan yang tepat dari kawat, isolasi kawat, dan material potting akan menghasilkan segel yang memuaskan antara termistor dan lingkungan eksternal.
13. Identifikasi Tanda
Thermistor yang selesai dapat ditandai untuk identifikasi yang mudah. Ini bisa sesederhana titik warna atau lebih kompleks, seperti kode tanggal dan nomor bagian. Dalam beberapa aplikasi, pewarna dapat ditambahkan ke lapisan pada tubuh thermistor untuk mendapatkan warna tertentu. Titik warna biasanya ditambahkan ke thermistor melalui proses imbasan. Gunakan pena tanda untuk menghasilkan label yang memerlukan karakter alfanumerik. Mesin ini hanya menggunakan tinta permanen untuk menandai bagian-bagian. Tinta tersebut mengeras pada suhu tinggi.
14. Pemeriksaan Akhir
Semua pesanan yang selesai akan diperiksa untuk cacat fisik dan listrik pada dasar "tanpa cacat". Semua parameter diperiksa dan dicatat sebelum produk meninggalkan pabrik.
15. Bungkus & Kirim Semua thermistor dan komponen dikemas dengan hati-hati dan akan digunakan oleh pelanggan.