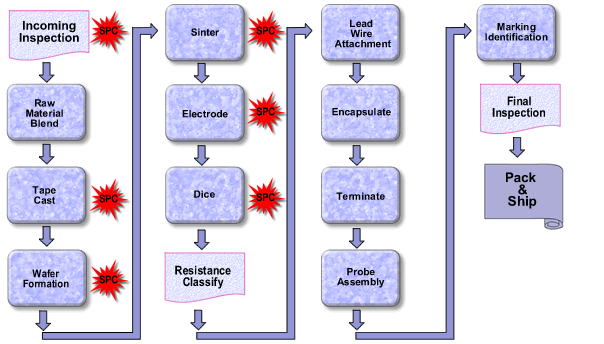
O proceso de fabricación de termistores NTC pode dividirse en: Inspección de Entrada – Mistura de Materiais Primarios – Laminado – Formación de Fais – Sinter – Electrodo – Dado – Clasificación de Resistencia – Fixación do Cable de Contacto – Encapsular – Terminar – Montaxe de Sonda – Identificación de Marcado – Inspección Final – Empaquetar e Enviar .
1. Inspección de Entrada
Todos os materiais primarios son inspeccionados ao recibir para verificar se as súas propiedades físicas e eléctricas son aceptables. Asignar un ID# único e usar o para a trazabilidade por lotes.
2. Mezcla de Materiais Primarios
A fabricación de termistores NTC comeza coa mezcla precisa dos materiais primarios en solucións de ligante orgánico. Estes materiais primarios son óxidos metálicos en polvo como manganeso, níquel, cobalto e óxido de cobre. Tamén se engaden outros estabilizadores á mezcla. Os óxidos e o ligante combinanse usando unha técnica chamada molienda esférica. No proceso de molienda esférica, os materiais son mezclados e o tamaño da partícula do polvo de óxido é reducido. A mezcla homoxénea terminada ten a consistencia dunha pasta espesa. A composición exacta de varios óxidos metálicos e estabilizadores determina as características de resistencia-temperatura e resistividade dos compónentes cerámicos cocidos.
3. Formado en Fita
O “lodo” distribúese nunha chapa de plástico en movemento empregando tecnoloxía de lama doctor. A espesura exacta do material controlase ajustando a altura da esponxa sobre a chapa de plástico, a velocidade da chapa e ajustando a viscosidade do lodo. O material de fundición sécase nunha correia de fundición plana a través dun forno túnel lonxano a alta temperatura. O resultado é unha fita “verde” maleable e fácil de formar. Despois realiza o control de calidade e análise na fita. A espesura da fita termistor varía entre 0,001” e 0,100” nunha ampla rexión, dependendo das especificacións específicas do compoñente.
4. Formación da wafer
A fita está pronta para ser formada en wafer. Cando se necesiten materiais finos, basta cortar a fita en pequenos cadrados. Para wafer máis grosos, corte a fita en cadrados e apíleos uns sobre outros. Estes wafer apilados son posteriormente laminados xuntos. Isto permite producir wafer coa grosor casi desexado. Despois, o wafer sofre unha proba adicional de calidade para asegurar unha alta uniformidade e calidade. Posteriormente, o wafer é sometido a un ciclo de eliminación do ligante. Este método retira a maior parte do ligante orgánico do wafer. Para prevenir estrés físico adverso no wafer do termistor, mantiense un control preciso do tempo/temperatura durante o ciclo de queima do adhesivo.
5. Sinter
A wafer é aquecida a unha temperatura moi alta nun ambiente oxidante. A estas altas temperaturas, os óxidos reaccionan entre si e fundense xuntos para formar unha matriz cerámica de spinelo. Durante o proceso de sinterización, o material densifícase ata un nivel predeterminado, e permítese que as fronteiras de grano da cerámica crezcan. Mantén un perfil de temperatura preciso durante o proceso de sinterización para evitar a fractura da wafer e asegurar a produción de cerámicas acabadas que podan producir pezas coñecaracterísticas eléctricas uniformes. Despois da sinterización, vólvese inspeccionar a calidade da wafer, e rexistranse as características eléctricas e físicas.
6. Electrodo
O contacto óhmico con discos cerámicos obtense empregando materiais de electrodo de filme espeso. O material é normalmente prata, paladio-prata, ouro ou platino, dependendo da aplicación. O material do electrodo consiste nunha mistura de metal, vidro e varios solventes, e aplícase nas dúas superficies opostas dun disco ou chip mediante serigrafiado, aspersión ou cepillado. O material do electrodo selle no interior dun forno de cinturón de filme espeso na cerámica, e forma a unión eléctrica e mecánica entre a cerámica e o electrodo. Despois, verifica o disco metalizado e rexistra as súas propiedades. Un control preciso no proceso do electrodo asegura que os componentes producidos a partir dos discos terán unha excelente fiabilidade a longo prazo.
7. Dados
A serra de corte de semicondutores de alta velocidade úsase para cortar o chip en pequenos chips. A roda de corte emprega unha roda de diamante e pode producir un gran número de díes extremadamente uniformes. O termistor resultante pode ser tan pequeno como 0,010 “a 1000”. A diferenza no tamaño do chip nun conxunto de chips de termistores é realmente imedible. Un termistor típico pode producir miles de chips de termistor. Despois do corte, limpase o chip e comprobanse as dimensións e as características eléctricas. As inspeccións eléctricas inclúen a determinación dos valores de resistencia nominais para aplicacións específicas, as características de resistencia-temperatura, a produtividade e a aceptabilidade do lote. A resistencia e as características de resistencia-temperatura midense con precisión dentro de 0,001 °C usando un control de temperatura preciso.
8. Clasificación de Resistencia
Todos os termistores son probados para comprobar os valores correctos de resistencia, normalmente a 25 °C. Estes chips son habitualmente testados automaticamente, pero tamén se poden probar manualmente en función da produción e especificacións. O procesador de chips automático está conectado a un dispositivo de prueba de resistencia e a un ordenador programado polo operador para colocar o chip en diversas áreas de memoria dependendo do seu valor de resistencia. Cada procesador de chips automático pode probar 9000 partes por hora de forma moi precisa.
9. Fixación do Cable de Contacto
En algúns casos, os termistores venén á venda na forma de chips e non requiren patas, pero na maioría dos casos requirense patas. O chip do termistor conectase ás patas mediante soldadura ou por contactos de presión no envoltorio do diodo. Durante o proceso de soldadura, o chip do termistor colócase no marco das patas, que depende da tensión elástica do alambre para manter o chip durante o proceso de soldadura. A ensamblaxe imerge entón nunha cuba coa solda fundida e retírase. A taxa de impregnación e o tempo de residencia controlanse precisamente para evitar un choque térmico excesivo ao termistor. Tamén empreganse fluxos especiais para mellorar a soldabilidade sen danar o chip do termistor. A solda fixa aos electrodos do chip e ás patas para proporcionar unha unión sólida entre o alambre e o chip. No caso do paquete tipo diodo “DO-35”, o chip do termistor mantiense entre as dúas patas dun xeito axial. A mangote de vidro colócase ao redor do compoñente e aquecese a alta temperatura. O vidro derrete ao redor do chip do termistor e sella á pata. Por exemplo, nunha estrutura de diodo, a presión exercida polo vidro sobre o módulo proporciona o contacto necesario entre o alambre da pata e o chip do termistor.
Os cables utilizados para termistores son normalmente de cobre, níquel ou liga, coa maioría das veces con revestimento de estaño ou chumbo. Poden empregarse materiais condutores de liga de baixa condutividade térmica en algúns aplicativos onde se require aislamento térmico entre o termistor e o conductor. En moitos aplicativos, isto permite que os termistores respondan máis rapidamente ás cambios de temperatura. Despois da unión, comproba a ligazón entre o cable e o chip. Unha interface de soldadura forte axuda a asegurar a fiabilidade a longo prazo do termistor completado.
10. Encapsular
Para protexer os termistores da atmosfera de funcionamento, humidade, ataques químicos e corrosión por contacto, os termistores con terminais son normalmente recubertos con un revestimento conformal protexedor. O sello é habitualmente unha resina epoxi con alta condutividade térmica. Outros selladores inclúen silicón, cemento cerámico, lixa, poliuretano e mangas retrácteis. Os sellantes tamén axudan a asegurar unha boa integridade mecánica do equipo. Debe considerarse a resposta térmica do termistor ao escoller materiais de embalaxe. En aplicaciones onde a resposta térmica rápida é crítica, empreganse filmes de selladores con alta condutividade térmica. Cando a protección ambiental é máis importante, pode seleccionarse outro sellante. Sellantes como a resina epoxi, o gel de silicio, o cemento cerámico, a lixa e o poliuretano son normalmente aplicados por impregnación e curados a temperatura ambiente ou colocados nun forno a temperaturas elevadas. Controlase con precisión o tempo, a temperatura e a viscosidade durante todo o proceso para asegurar que non se desenvolven poros ou outras deformidades.
11. Terminar
Os termistores suelen equiparse con terminais conectados ao extremo dos seus conductores. Antes de aplicar o terminal, a isolación do cable conductor é debidamente descuberta para adaptarse ao terminal especificado. Estes terminais conectanse aos cables empregando unha máquina de aplicación de ferramenta especial. Os terminais poden inserirse despois nunha carcasa de plástico ou metal antes de ser enviados ao cliente.
12. Montaxe de sonda
Por razoñs de protección ambiental ou mecánicas, os termistores normalmente están inmersos no caso da sonda. Estas envoltorías poden fabricarse en materiais como o epoxi, vinilo, acero inoxidable, aluminio, bronce e plástico. Ademais de proporcionar un montaxe mecánico adecuado para os elementos termistor, a envoltoría protexeos do ambiente ao que están expostos. A selección correcta dos materiais de conductor, isolante do fío e encapsulado provocará un selado satisfactorio entre o termistor e o ambiente externo.
13. Identificación de marca
O termistor terminado pode ser marcado para unha identificación fácil. Isto pode ser tan simple como puntos de cor ou máis complexo, como códigos de data e números de parte. En algúns aplicativos, pódense engadir corantes á cobertura do corpo do termistor para obter unha cor específica. Os puntos de cor solen addedos ao termistor mediante un proceso de impregnación. Emprega un marcador para xerar etiquetas que requiren caracteres alfanuméricos. Esta máquina só emprega tinta permanente para marcar as pezas. A tinta solidíficase a unha temperatura elevada.
14. Inspección Final
Todas as órdenes completadas serán inspeccionadas en busca de defectos físicos e eléctricos nunha base de "sen defectos". Todos os parámetros son comprobados e rexistrados antes de que o produto saia da fábrica.
15. Embalar e Enviar Todos os termistores e compoñentes son embalados con cuidado e serán usados polos clientes.