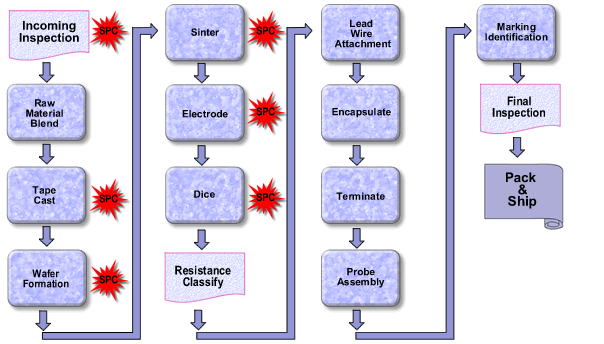
Der Fertigungsprozess von NTC-Thermistoren kann unterteilt werden in: Eingangskontrolle – Rohstoffmischung – Bandschichtung – Waferherstellung – Sinter – Elektrode – Würfel – Widerstandsklassifizierung – Anschluss der Leitung – Kapseln – Beenden – Sondebau – Kennzeichnungserkennung – Endprüfung – Packen & Versand .
1. Eingangskontrolle
Alle Rohstoffe werden bei Lieferung geprüft, um deren physikalische und elektrische Eigenschaften zu überprüfen. Weisen Sie eine eindeutige ID# zu und verwenden Sie sie für die Chargenverfolgbarkeit.
2. Rohstoffmischung
Die Herstellung von NTC-Thermistoren beginnt mit der präzisen Mischung von Rohstoffen in organischen Bindemittel-Lösungen. Diese Rohstoffe sind gepulverte Übergangsmetalloxide wie Mangan, Nickel, Kobalt und Kupferoxid. Auch andere Stabilisatoren werden zur Mischung hinzugefügt. Die Oxide und das Bindemittel werden unter Verwendung einer feuchten Prozessmethode namens Ballmahlung vermischt. Beim Ballmahlprozess werden die Materialien gemischt und die Partikelgröße des Oxidpulvers wird reduziert. Das fertige homogene Gemisch hat die Konsistenz eines dicken Breis. Die genaue Zusammensetzung der verschiedenen Metalloxide und Stabilisatoren bestimmt die Widerstand-Temperatur-Charakteristiken und die Leitfähigkeit der gebrannten keramischen Komponenten.
3. Bandguss
Die „Schlamm“-Mischung wird auf einer beweglichen Kunststoffträgerfolie mittels Doktorblatt-Technologie verteilt. Die exakte Materialdicke wird durch die Einstellung der Höhe des Schabers über der Kunststoffträgerfolie, die Geschwindigkeit der Trägerfolie und durch die Anpassung der Viskosität des Schlammes kontrolliert. Das Gussmaterial wird in einem langen Tunnelofen bei hoher Temperatur auf einer flachen Gussband getrocknet. Das resultierende „grüne“ Band ist formbar und leicht zu verformen. Anschließend werden Qualitätskontrollen und Analysen am Band durchgeführt. Die Dicke des Thermistorbands variiert je nach spezifischen Komponentenspezifikationen in einem breiten Bereich von 0,001“ bis 0,100“.
4. Waferschaffung
Die Bahn ist bereit, zu Wafers geformt zu werden. Wenn dünne Materialien benötigt werden, schneidet man einfach die Bahn in kleine Quadrate. Für dickere Wafers schneidet man die Bahn in Quadrate und stapelt sie aufeinander. Diese gestapelten Wafers werden dann zusammen verleimt. Dadurch können wir Wafers fast beliebiger Dicke herstellen. Anschließend unterzieht sich der Wafer weiteren Qualitätsprüfungen, um eine hohe Gleichmäßigkeit und Qualität sicherzustellen. Danach wird der Wafer einem Binder-Ausbrandzyklus unterzogen. Diese Methode entfernt den größten Teil des organischen Binders vom Wafer. Um unerwünschte mechanische Belastungen des Thermistor-Wafers zu vermeiden, wird während des Klebstoff-Verbrennungskreislaufes eine präzise Zeit-/Temperaturregelung eingehalten.
5. Sintern
Die Wafer wird in einer oxidierenden Atmosphäre auf eine sehr hohe Temperatur erhitzt. Bei diesen hohen Temperaturen reagieren die Oxide miteinander und verschmelzen zu einem Spinel-Keramik-Matrix. Während des Sinterprozesses wird das Material auf ein vorgegebenes Maß verdichtet, und die Korn grenzen der Keramik können sich ausbilden. Halten Sie ein präzises Temperaturprofil während des Sinterprozesses ein, um Waferrisse zu vermeiden und sicherzustellen, dass fertige Keramiken hergestellt werden, die Bauteile mit einheitlichen elektrischen Eigenschaften erzeugen können. Nach dem Sintern wird die Qualität der Wafer erneut überprüft, und die elektrischen und physikalischen Eigenschaften werden dokumentiert.
6. Elektrode
Der ohmische Kontakt mit keramischen Wafers wird durch das Verwenden von Dickenfilm-Elektrodenmaterialien hergestellt. Das Material ist in der Regel Silber, Palladiumsilber, Gold oder Platin, je nach Anwendung. Das Elektrodenmaterial besteht aus einer Mischung aus Metall, Glas und verschiedenen Lösemitteln und wird auf die beiden gegenüberliegenden Flächen einer Wafer oder Chip durch Silk-Screen-Druck, Sprühen oder Pinseln aufgetragen. Das Elektrodenmaterial wird in einem Dickenfilm-Bandofen auf der Keramik gebrannt, und eine elektrische Verbindung sowie eine mechanische Kombination zwischen der Keramik und dem Elektroden entsteht. Danach wird die metallisierte Wafer überprüft und die Eigenschaften dokumentiert. Eine präzise Kontrolle im Elektrodenprozess stellt sicher, dass die aus Wafers hergestellten Komponenten eine exzellente Langzeitzuverlässigkeit haben werden.
7. Würfel
Die Hochgeschwindigkeits-Halbleiter-Schneidsäge wird verwendet, um den Chip in kleinere Chips zu schneiden. Die Sägeblätter verwenden Diamantklingen und können eine große Anzahl von extrem gleichmäßigen Würfeln erzeugen. Der resultierende Thermistorchip kann so klein wie 0,010 „bis 1000“ sein. Die Größeunterschiede einer Gruppe von Thermistorchips sind tatsächlich unermesslich. Ein typischer Thermistorchip kann Tausende von Thermistorchips produzieren. Nach dem Schneiden wird der Chip gereinigt und die Abmessungen sowie die elektrischen Eigenschaften überprüft. Elektrische Prüfungen umfassen die Bestimmung der Nennwiderstandswerte für spezifische Anwendungen, Widerstandstemperaturcharakteristiken, Produktionsausbeute und Chargenakzeptanz. Widerstand und Widerstandstemperaturcharakteristiken werden bei präziser Temperaturregelung auf 0,001 °C genau gemessen.
8. Widerstands-Klassifizierung
Alle Thermistoren werden auf korrekte Widerstandswerte getestet, meistens bei 25 °C. Diese Chips werden normalerweise automatisch getestet, aber sie können auch manuell getestet werden, je nach Produktion und Spezifikationen. Der automatische Chip-Prozessor ist mit einem Widerstandstestgerät und einem von dem Bediener programmierten Computer verbunden, um den Chip je nach seinem Widerstandswert in verschiedene Speicherbereiche zu sortieren. Jeder automatische Chip-Prozessor kann 9000 Teile pro Stunde mit hoher Genauigkeit testen.
9. Anbringung der Leitungsdrähte
In manchen Fällen werden Thermistoren in Form von Chips verkauft und erfordern keine Anschlüsse, aber in den meisten Fällen sind Anschlüsse erforderlich. Der Thermistorchip wird mit den Anschlüssen durch Löten oder durch Druckkontakte im Diodengehäuse verbunden. Während des Lötvorgangs wird der Thermistorchip auf das Anschlussgestell geladen, das von der Federkraft des Drahtes abhängt, um den Chip während des Lötvorgangs zu halten. Die Montage wird dann in den geschmolzenen Lötzinnbehälter getaucht und wieder entfernt. Die Impregniergeschwindigkeit und die Verweildauer werden genau gesteuert, um einen übermäßigen thermischen Schock für den Thermistor zu vermeiden. Spezielle Flüsse werden auch verwendet, um die Löseigenschaften zu verbessern, ohne den Thermistorchip zu beschädigen. Das Lötzinn haftet an den Elektroden des Chips und führt zu einem festen Draht-Chip-Bindung. Bei dem Diode-Typ „DO-35“ Gehäuse ist der Thermistorchip axial zwischen den beiden Anschlüssen positioniert. Eine Glasmanschette wird um das Bauteil gelegt und bei hoher Temperatur erhitzt. Die Glasmanschette schmilzt um den Thermistorchip herum und wird am Anschluss versiegelt. Zum Beispiel übt das Glas in einer Diodenstruktur Druck auf das Modul aus, um den notwendigen Kontakt zwischen dem Anschlussdraht und dem Thermistorchip zu gewährleisten.
Die für Thermistoren verwendeten Leiter bestehen in der Regel aus Kupfer, Nickel oder Legierung und werden oft mit Zinn oder Lötzinn überzogen. In einigen Anwendungen können Legierungsmaterialien mit geringer thermischer Leitfähigkeit eingesetzt werden, wenn eine thermische Isolation zwischen Thermistor und Leiter erforderlich ist. In den meisten Anwendungen ermöglicht dies den Thermistoren, schneller auf Temperaturänderungen zu reagieren. Nach dem Anbringen sollte die Verbindung zwischen Leiter und Chip überprüft werden. Eine starke Schweißnaht trägt zur Sicherstellung der langfristigen Zuverlässigkeit des fertigen Thermistors bei.
10. Kapseln
Um Thermistoren vor der Wirkstoffatmosphäre, Feuchtigkeit, chemischem Angriff und Kontaktkorrosion zu schützen, werden Leiterbahnen-Thermistoren normalerweise mit einem schützenden konformen Beschichtungsmaterial überzogen. Das Dichtungsmaterial ist in der Regel ein epoxyharziges Material mit hoher Wärmeleitfähigkeit. Andere Dichtungsmaterialien umfassen Silikon, keramischen Zement, Farbe, Polyurethan und Schrumpffolie. Dichtungen tragen auch dazu bei, die mechanische Integrität der Ausrüstung sicherzustellen. Die thermische Reaktionszeit des Thermistors sollte bei der Auswahl von Verpackungsmaterialien berücksichtigt werden. In Anwendungen, in denen eine schnelle thermische Reaktionszeit entscheidend ist, werden Filme aus Dichtungsmaterialien mit hoher Wärmeleitfähigkeit verwendet. Wenn der Umweltschutz wichtiger ist, kann ein anderes Dichtungsmaterial ausgewählt werden. Dichtungsmaterialien wie Epoxyharz, Silikonkautschuk, keramischer Zement, Farbe und Polyurethan werden normalerweise durch Impregnation aufgetragen und bei Raumtemperatur oder in einem Ofen bei erhöhten Temperaturen geerdet. Genau dosierte Zeiten, Temperaturen und Viskositätskontrollen werden während des gesamten Prozesses angewendet, um sicherzustellen, dass keine Porosität oder andere Verformungen auftreten.
11. Beenden
Thermistoren sind normalerweise mit Terminalen ausgestattet, die an das Ende ihrer Anschlussdrähte geklebt sind. Bevor das Terminal angebracht wird, wird die Isolation des Leitungsdrats ordnungsgemäß abgeschält, um dem vorgesehenen Terminal zu entsprechen. Diese Terminalen werden mit einer speziellen Werkzeuganwendungsmaschine an die Drähte angeschlossen. Die Terminalen können dann in eine Kunststoff- oder Metallgehäuse eingefügt werden, bevor sie an den Kunden geliefert werden.
12. Probiermontage
Aus Umweltschutz- oder mechanischen Gründen werden Thermistoren in der Regel in den Sondegehäuse eingebracht. Diese Gehäuse können aus Materialien wie Epoxy, Vinyl, Edelstahl, Aluminium, Messing und Kunststoff hergestellt werden. Neben der Bereitstellung einer geeigneten mechanischen Befestigung für die Thermistorelemente schützt das Gehäuse sie vor der Umgebung, der sie ausgesetzt sind. Die richtige Auswahl von Anschlussdrähten, Kabelisolation und Füllmaterial führt zu einem zufriedenstellenden Dichtung zwischen dem Thermistor und der äußeren Umgebung.
13. Kennzeichnungserkennung
Der fertige Thermistor kann zur einfacheren Identifizierung markiert werden. Dies kann so einfach wie Farbpunkte oder komplexer sein, wie Datumscode und Teilenummer. In einigen Anwendungen können Farbstoffe in die Beschichtung des Thermistor-Körpers gegeben werden, um eine bestimmte Farbe zu erhalten. Die Farbpunkte werden normalerweise durch einen Impregnierungsprozess auf den Thermistor aufgetragen. Verwenden Sie einen Marker, um Etiketten mit alphanumerischen Zeichen zu erstellen. Diese Maschine verwendet nur dauerhaftes Tinte, um Teile zu kennzeichnen. Die Tinte festigt sich bei erhöhter Temperatur.
14. Endprüfung
Alle abgeschlossenen Aufträge werden auf physische und elektrische Mängel hin geprüft, basierend auf dem 'Null-Mangel'-Prinzip. Alle Parameter werden überprüft und dokumentiert, bevor das Produkt das Werk verlässt.
15. Verpacken & Versand Alle Thermistoren und Komponenten werden sorgfältig verpackt und werden von Kunden genutzt.