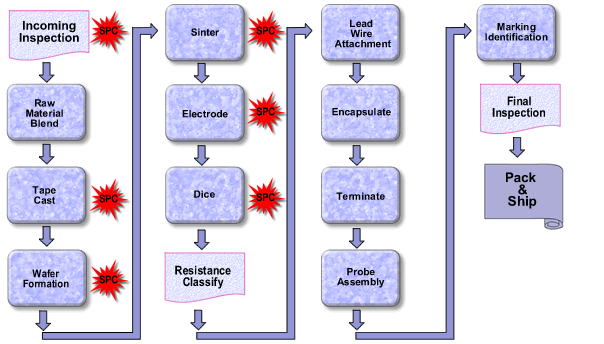
Процесът на производство на NTC термистор може да се раздели на: Входна проверка – Смесване на суровини – Лентовидно формуване – Формиране на плочки – Пресечен – електрод – Зарби – Класификация на съпротивата – Прикрепяне на водещи жици – Обвиване – Терминиране – Съставка на зонд – Маркиране и идентификация – крайна проверка – Упаковка и доставка .
1. Входящ контрол
Всички суровини се проверяват при получаването, за да се потвърди дали техните физически и електрически свойства са приемливи. Присвояване на уникален ID# и неговото използване за проследимост на партията.
2. Смесване на сурови материали
Производството на NTC термистори започва с прецизно смесване на суровите материали в органични биндерни решения. Тези сурови материали са прахове от транзиционни метални оксиди като манган, никел, кобалт и меден оксид. Към сместа се добавят и други стабилизатори. Оксидите и байнера се комбинират чрез мокър процес, известен като топкено измиване. При този процес материалите се смесват, а размерът на частиците на оксидния прах се намалява. Готовата хомогенно смесена смес има консистентността на гъст прах. Точното съставление на различните метални оксиди и стабилизатори определя резистивните-температурни характеристики и резистивността на обгаряните керамични компоненти.
3. Лентова отливка
„Сместа“ се разпределя върху движещ се пластиков носител чрез технология на доктор лезие. Точната толщина на материалите се регулира чрез корекция на височината на шкрякала над пластиковия носител, скоростта на носителя и чрез корекция на вискозността на сместа. Материалът за отливки се сушува върху плосък пояс за отливки през дълга тунелна печка при висока температура. Резултиращата „зелена“ лента е пластична и лесно формируема. След това се провежда проверка на качеството и анализ на лентата. Толщината на термисторната лента се намира в широк диапазон между 0,001″ и 0,100″, като зависи от спецификациите на конкретния компонент.
4. Образуване на кристални пластинки
Лентата е готова да бъде формирана в плочки. Когато се нуждаем от тънки материали, просто разрязваме лентата на малки квадратчета. За по-дебели плочки, разрязваме лентата на квадрати и я слагаме един върху друг. Тези навлечени плочки после се ламинарат заедно. Това ни позволява да производим плочки с почти необходимата дебелина. След това, плочката преминава през допълнителни тестове за качество, за да се гарантира висока равномерност и качество. Последователно, плочката подлежи на цикъл за изгаряне на клея. Този метод премахва повечето от органичния клей от плочката. За да се предотвратят неблагоприятни физически стресове върху термисторната плочка, се поддържа точен контрол върху времето/температура по време на цикъла за изгаряне на клея.
5. Синтериране
Плитката се нагрява до много висока температура в окислителна атмосфера. При тези високи температури оксидите реагират помежду си и се спаяват заедно, образувайки матрица от спинелов керамичен материал. През процеса на спаяване материалът се уплътнява до предварително определен ниво, а граничните повърхности на керамика се разрешава да растат. Запазете точен температурен профил по време на процеса на спаяване, за да се избегне скъсването на плитката и да се гарантира производството на готови керамически изделия, които могат да произвеждат части с еднородни електрически характеристики. След спаяването качеството на плитката се проверява отново, а електрическите и физическите характеристики се записват.
6. Електрод
Охмовият контакт с керамични плочи се получава чрез използване на материал за тънък слой. Материалът обикновено е сребро, паладиево сребро, злато или платина, в зависимост от приложението. Материалът за електрод се състои от смес от метал, стъкло и различни растворители и се нанася на двете противоположни повърхности на плочка или чип чрез скрийното тиснење, бутушене или мазане. Материалът за електрод се спече на керамика в печка за тънък слой, като се образуват електрическото съединение и механичното комбиниране между керамиката и електрода. След това се проверява металализираната плоча и се записват свойствата. Точен контрол в процеса на електродите гарантира, че компонентите, произведени от плочите, ще имат отлична дългосрочна надеждност.
7. Зарчета
Високоскоростната полупроводниковa пилка се използва за разрязване на чипа на по-малки чипове. Пилката използва диамантна пилка и може да произведе голямо количество екстремно равномерни умиращи елементи. Резултатът термисторен чип може да е толкова малък, колкото 0,010“ до 1000”. Разликата в размерите на чиповете от един набор термисторни чипове всъщност е непомерима. Типичен термисторен чип може да произведе хиляди термисторни чипове. След разрязването, чипът се очистява и се проверяват размерите и електрическите характеристики. Електрическите проверки включват определянето на номиналните съпротивления за специфични приложения, съпротивление температурни характеристики, производствена дадност и приемливост на партията. Съпротивлението и характеристиките му спрямо температурата се измерват точно в рамките на 0,001 °C, като се използва прецизен температурен контрол.
8. Класификация на съпротивлението
Всички термистори се тестват за правилните стойности на съпротивлението, обикновено при 25 ° C. Тези чипове обикновено се тестват автоматично, но могат също да бъдат тествани ръчно в зависимост от производството и спецификациите. Автоматичният чип процесор е свързан с устройство за тест на съпротивлението и компютър, програмиран от оператора, за да поставя чипа в различни паметни области, зависещи от неговата стойност на съпротивлението. Всякъде автоматичен чип процесор може да тестира 9000 части на час по много точен начин.
9. Прикрепяне на проводника
В някои случаи термисторите се продават във вид чипове и не изискват жици, но в повечето случаи жиците са необходими. Термисторният чип се свързва с жиците чрез паяне или чрез контакт под налягане в диодния корпус. По време на процеса на паяне, термисторният чип се поставя на жицата, която зависи от пружинното напрежение на провода, за да задържи чипа по време на паянето. След това съставът се изпълнява в топена паяна маса и се премахва. Температурната скорост на проникване и времето на пребиваване са точно контролирани, за да се избегне прекалено термично шокиране на термистора. Използват се специални флюси, които усилват способността за паяне без да повредят термисторния чип. Паялото се прикрепя към електродите на чипа и водещите жици, за да се осигури прочен връз между провода и чипа. За диодния тип „DO-35“ корпус на термистора, термисторният чип се държи между двата водещи жички по аксиален начин. Стъкленият щит се поставя около компонента и се затопля до висока температура. Стъкленият щит се топи около термисторния чип и се запечатва към жицата. Например, в диодна конструкция, налягането, оказвано от стъклото върху модула, осигурява необходимия контакт между водещия провод и термисторния чип.
Кондукторите, използвани за термистори, обикновено са от мед, никел или сплав, обикновено с оловена или паяна покритие. При някои приложения могат да се използват материали за проводник с ниска термична проводимост, когато е необходима термична изолация между термистора и проводника. В повечето приложения това позволява на термисторите да реагират по-бързо на промени в температурата. След прикрепването проверете свързването между кондуктора и чипа. Силна сварваща повърхност помага да се гарантира продължителната надеждност на завършените термистори.
10. Инкапсулиране
За да се защитят термисторите от работна атмосфера, влажност, химически атаки и корозия на контакта, тоководните термистори обикновено са покрити с защитно конформно покритие. Запечатващият материал обикновено е епоксиден лак с висока термична проводимост. Други запечатващи материали включват силикон, керамичен цемент, боя, полиуретан и съкратима оплетка. Запечатващите материали също помагат да се осигури добра механична целостност на оборудването. Термичния отговор на термистора трябва да се има предвид при избора на упаковачни материали. В приложенията, където бързият термичен отговор е критичен, се използват плевели от запечатващи материали с висока термична проводимост. Когато защитата от околната среда е по-важна, може да се избере друг запечатващ материал. Запечатващите материали като епоксиден лак, силиконов гел, керамичен цемент, боя и полиуретан обикновено се нанасят чрез пропитване и се засичат при стаяна температура или се поставят в печка при повишени температури. През цял процес се използват точен контрол на времето, температурата и вискозитета, за да се гарантира, че не се развијат пиноли или други деформации.
11. Терминиране
Термисторите обикновено са оснащени с терминали, свързани с края на техните жици. Преди да бъде приложен терминалът, изолацията на жицата е правилно извадена, за да се подхожда за указания терминал. Тези терминали се свързват с жиците чрез специална машина за прилагане на инструменти. Терминалите после могат да бъдат вмъкнати в пластмасов или метален корпус преди да бъдат доставени на клиента.
12. Монтаж на зонд
За целите на защитата на околната среда или механически причини, термисторите обикновенно се погружават в корпуса на зонда. Тези ограждания могат да се изготвят от материали, включително епоксид, винил, неръжавееща стомана, алуминий, мед и пластмаса. Освен че предоставят подходящо механично закрепяване за термисторните елементи, ограждането ги защитава от околната среда, на която са изложени. Правилният избор на проводник, изолацията на държача и материалите за запечатване ще резултира в удовлетворително затваряне между термистора и външната среда.
13. Маркировка и идентификация
Готовият термистор може да бъде маркиран за лесна идентификация. Това може да е толкова просто, колкото цвятни точки, или по-сложно, като дати на производство и номера на част. В някои приложения могат да се добавят бои към облагането на корпуса на термистора, за да се получи определен цвят. Цветните точки обикновено се добавят към термистора чрез процес на импрегниране. Използвайте маркер, за да генерирате етикети, които изискват буквоцифрови символи. Тази машина използва само постоянни чернила за маркиране на части. Червенцата се затвърдява при висока температура.
14. Крайна проверка
Всички завършени поръчки ще бъдат проверени за физически и elektricheski дефекти по принцип „без дефекти“. Всички параметри се проверяват и записват преди продукта да напусне фабриката.
15. Упаковка и доставка Всички термистори и компоненти са внимателно упаковани и ще бъдат използвани от клиентите.