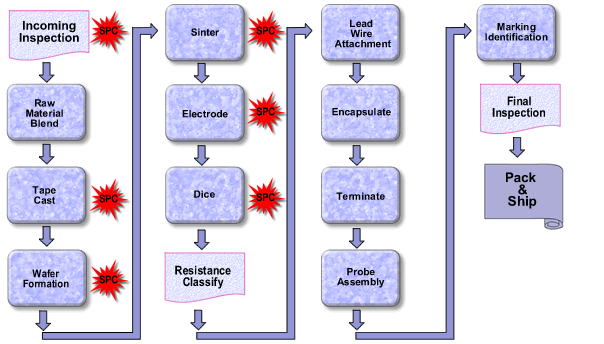
يمكن تقسيم عملية تصنيع المقاوم الحراري من نوع NTC إلى: الفحص الوارد – خلط المواد الخام – تشكيل الشريط – تكوين البلاستير – مُحَمَّص – القطب الكهربائي – النرد – تصنيف المقاومة – تثبيت سلك القيادة – التغليف – الإنهاء – تركيب البروب – التعرف على العلامات – الفحص النهائي – التعبئة والشحن .
1. الفحص الوارد
تفحص جميع المواد الخام عند الاستلام للتحقق مما إذا كانت خصائصها الفيزيائية والكهربائية مقبولة. قم بتعيين رقم تعريف فريد واستخدمه لتتبع الدفعة.
2. خليط المواد الخام
تبدأ عملية تصنيع مقاومات NTC الحرارية بدقة في خلط المواد الخام مع حلول رابطة عضوية. تشمل هذه المواد الخام أكاسيد المعادن الانتقالبة المسحوقة مثل المنغنيز، النيكل، الكوبالت وأكسيد النحاس. يتم إضافة مثبتات أخرى أيضًا إلى الخليط. يتم دمج أكسيد الرابطة باستخدام تقنية تُسمى الطحن الكروي الرطب. في عملية الطحن الكروي، يتم خلط المواد وتقليل حجم جزيئات بودرة الأكسيد. يمتلك الخليط المتجانس النهائي قوام العجينة السميكة. التركيبة الدقيقة لأكاسيد المعادن المختلفة والمثبتات تحدد خصائص المقاومة-درجة الحرارة والمقاومة الكهربائية للمكونات السيراميكية المحترقة.
3. صب الشريط
يتم توزيع "العجينة" على ورقة حاملة بلاستيكية متحركة باستخدام تقنية شفرة الطبيب. يتم التحكم في سماكة المادة بدقة عن طريق ضبط ارتفاع الممسحة فوق ورقة الحامل البلاستيكية، وسرعة ورقة الحامل، وضبط لزوجة العجينة. يتم تجفيف المادة المرسومة على حزام رسم مسطح من خلال فرن نفق طويل عند درجة حرارة عالية. الناتج هو شريط "أخضر" قابل للتشكيل وسهل التشكيل. ثم يتم إجراء فحص الجودة وتحليل الشريط. تتراوح سماكة شريط المقاوم الحراري بين 0.001 بوصة إلى 0.100 بوصة في نطاق واسع، وذلك بناءً على مواصفات المكونات المحددة.
4. تكوين الوافر
الشريط جاهز ليتم تشكيله إلى أقراص. عند الحاجة إلى مواد رقيقة، قم بقص الشريط إلى مربعات صغيرة.而对于أقراص أسمك، قم بقص الشريط إلى مربعات ورصها فوق بعضها البعض. يتم لamination هذه الأقراص المكدسة معًا. هذا يتيح لنا إنتاج أقراص بالسماكة المطلوبة تقريبًا. بعد ذلك، تخضع القرص لاختبارات جودة إضافية لضمان التجانس والجودة العالية. ثم يتم تعريض القرص لدورة حرق الربط.此الطريقةتزالمعظم من المواد العضوية الملتصقة من القرص. للحفاظ على استقرار الضغط الفيزيائي للقرص الحراري، يتم الحفاظ على التحكم الدقيق في الزمن/الدرجة الحرارية أثناء دورة حرق الربط.
5. السinter
يُسخن الوشاح إلى درجة حرارة مرتفعة جدًا في غلاف أكسدي. عند هذه الدرجات العالية من الحرارة، تتفاعل الأكاسيد مع بعضها البعض وتندمج لتشكيل مصفوفة سيراميك من نوع السبينل. أثناء عملية التصلب (السينترينج)، يتم تكثيف المادة إلى مستوى محدد مسبقًا، ويُسمح بنمو حدود الحبيبات للسيراميك. يجب الحفاظ على ملف درجة حرارة دقيق خلال عملية التصلب لتجنب كسر الوشاح وضمان إنتاج سيراميك نهائي يمكنه تصنيع أجزاء ذات خصائص كهربائية موحدة. بعد التصلب، يتم فحص جودة الوشاح مرة أخرى، وتسجل الخصائص الكهربائية والفيزيائية.
6. القطب الكهربائي
يتم الحصول على الاتصال الأومي مع الشرائح السيراميكية باستخدام مواد الكهرباء السميكة. عادةً ما تكون المادة الفضية، فضية الباذلديوم، ذهبية أو بlatinum حسب التطبيق. تتكون مادة الكهرباء من خليط من المعدن، الزجاج والمحاليل المختلفة، وتُطبق على السطحين المتقابلين لشريحة أو رقاقة بواسطة الطباعة الشبكية، الرش أو الفرشاة. يتم حرق مادة الكهرباء على السيراميك في أفران الحز السميكة، ويتم تشكيل الاتصال الكهربائي والتركيب الميكانيكي بين السيراميك والكهرباء. ثم يتم فحص الشريحة المعدنية وتسجيل الخصائص. يضمن التحكم الدقيق في عملية الكهرباء أن تكون المكونات المنتجة من الشرائح ذات موثوقية طويلة الأمد ممتازة.
7. قطع النرد
تُستخدم منشار شبه الموصلات السريع لقص الشرائح الكبيرة إلى شرائح صغيرة. تستخدم قطعة المنشار شفرة ماسية ويمكنها إنتاج عدد كبير من الأقراص المتساوية بشكل متطرف. يمكن أن تكون الشريحة الناتجة للثرمستور صغيرة جدًا مثل 0.010 "إلى 1000". اختلاف حجم الشريحة في مجموعة من الشرائح يكون فعليًا غير قابل للقياس. يمكن لإحدى الشرائح النموذجية إنتاج آلاف أشباه الموصلات. بعد القص، يتم تنظيف الشريحة وفحص الأبعاد والخصائص الكهربائية. تتضمن الفحوصات الكهربائية تحديد القيم المقاومة الاسمية لمجموعة التطبيقات معينة، خصائص درجة الحرارة للمقاومة، نسبة الإنتاج، وقبول الدفعة. يتم قياس المقاومة وخصائص المقاومة مع درجة الحرارة بدقة داخل 0.001 ° C باستخدام التحكم الدقيق بدرجة الحرارة.
8. تصنيف المقاومة
يتم اختبار جميع المقاومات الحرارية لقيم المقاومة الصحيحة، عادةً عند 25 °م. يتم اختبار هذه الشرائح عادةً تلقائيًا، لكن可以从 أيضًا يدويًا بناءً على الإنتاج والمواصفات. يتم توصيل معالج الشريحة التلقائي بجهاز اختبار المقاومة وكمبيوتر مبرمج من قبل المشغل لوضع الشريحة في مناطق ذاكرة مختلفة بناءً على قيمتها المقاوِمة. يمكن لكل معالج شريحة تلقائي اختبار 9000 قطعة في الساعة بطريقة دقيقة جدًا.
9. تثبيت سلك الرصاص
في بعض الحالات، يتم بيع المقاومات الحرارية على شكل رقائق ولا تحتاج إلى أسلاك، لكن في معظم الحالات تكون الأسلاك ضرورية. يتم توصيل الرقاقة المقاومة حراريًا بالأسلاك عن طريق اللحام أو بواسطة اتصالات ضغط داخل غلاف الديود. أثناء عملية اللحام، يتم وضع الرقاقة المقاومة حراريًا على إطار الأ lead frame، والذي يعتمد على قوة مرونة السلك لدعم الرقاقة أثناء عملية اللحام. بعد ذلك، يتم غمر التجميعة في وعاء اللحام المنصهر وإخراجها. يتم التحكم بدقة في معدل النفاذية ومدة الإقامة لتجنب الصدمات الحرارية المفرطة للمقاومة الحرارية. كما تُستخدم معاجين خاصة لتحسين قابلية اللحام دون تلف الرقاقة المقاومة حراريًا. يلتحم اللحام بمداخل الرقاقة والأسلاك لتوفير رابط قوي بين السلك والرقاقة. بالنسبة للحزمة من نوع "DO-35" التي تحتوي على مقاومة حرارية، فإن الرقاقة المقاومة حراريًا توضع بين السلكين بشكل محوري. يتم وضع الجراب الزجاجي حول المكون وتسخينه إلى درجة حرارة عالية. يذوب الجراب الزجاجي حول الرقاقة المقاومة حراريًا ويتم إغلاقه على السلك. على سبيل المثال، في هيكل الديود، فإن الضغط الذي تمارسه الزجاجة على الوحدة يوفر الاتصال اللازم بين سلك الاتصال والرقاقة المقاومة حراريًا.
تُستخدم السدادات المستخدمة في المقاومات الحرارية عادةً النحاس أو النيكل أو السبائك، وغالبًا ما تكون مغلفة بطلاء من القصدير أو اللحام. يمكن استخدام مواد موصلات ذات سبيكة قليلة التوصيل الحراري في بعض التطبيقات حيث يكون هناك حاجة للعزل الحراري بين المقاومة الحرارية والموصل. في معظم التطبيقات، يسمح هذا للمقاومات الحرارية بالاستجابة لتغيرات درجة الحرارة بشكل أسرع. بعد التثبيت، تحقق من ربط السلك مع الرقاقة. يساعد اتصال لحام قوي في ضمان موثوقية طويلة الأجل للمقاومة الحرارية المكتملة.
10. تغليف
من أجل حماية المقاومات الحرارية (thermistors) من التأثيرات البيئية، الرطوبة، الهجمات الكيميائية والتآكل الناتج عن الاتصال، يتم عادةً تغليف المقاومات الحرارية بطبقة واقية مطابقة. المادة الختمية تكون عادة من راتنج الإيبوكسي ذي الموصلية الحرارية العالية. تتضمن مواد الختم الأخرى السيليكون، الإسمنت السيراميكي، الطلاء، البولي يوريثين والكمامة القابلة للانكماش. تسهم مواد الختم أيضًا في ضمان سلامة الجهاز الميكانيكية. يجب أخذ استجابة المقاومة الحرارية عند اختيار مواد التغليف بعين الاعتبار. في التطبيقات التي يكون فيها الاستجابة الحرارية السريعة أمرًا حاسمًا، يتم استخدام أغلفة من مواد ختم ذات موصلية حرارية عالية. أما عندما يكون الحماية البيئية أكثر أهمية، يمكن اختيار نوع آخر من مواد الختم. يتم طلاء مواد الختم مثل راتنج الإيبوكسي، السيليكا جل، الإسمنت السيراميكي، الطلاء، والبولي يوريثين عادةً بالتشبع (impregnation) وتُجفف عند درجة حرارة الغرفة أو توضع في فرن عند درجات حرارة مرتفعة. يتم استخدام تحكم دقيق في الزمن، درجة الحرارة واللزوجة طوال العملية لضمان عدم تطور الثقوب أو تشوهات أخرى.
11. إنهاء
يتم تجهيز المقاومات الحرارية عادةً بمحابس متصلة بنهاية أسلاكها. قبل تركيب المفصل، يتم إزالة العازل عن سلك القيادة بشكل صحيح ليناسب المفصل المحدد. يتم ربط هذه المحابس بالأسلاك باستخدام آلة تطبيق أدوات خاصة. يمكن بعد ذلك إدراج المحابس في غلاف بلاستيكي أو معدني قبل تسليمها إلى العميل.
12. تجميع الاستشعار
لأغراض حماية البيئة أو الميكانيكية، يتم عادة غمر المقاومات الحرارية داخل غلاف الاستشعار. يمكن تصنيع هذه الأغلفة من مواد تشمل الإيبوكسي، الفينيل، الفولاذ المقاوم للصدأ، الألومنيوم، النحاس الأصفر والبلاستيك. بالإضافة إلى توفير تركيب ميكانيكي مناسب لعناصر المقاومة الحرارية، فإن الغلاف يحميهم من البيئة التي يتعرضون لها. ستؤدي الاختيار الصحيح للمواد المستخدمة في السلك، عزل الأسلاك ومواد التثبيت إلى تحقيق ختم مناسب بين المقاومة الحرارية والبيئة الخارجية.
13. تحديد العلامات
يمكن وضع علامات على المقاومة الحرارية النهائية لتسهيل التعرف عليها. يمكن أن تكون هذه العلامات بسيطة مثل نقاط ألوان أو أكثر تعقيدًا، مثل أكواد التاريخ وأرقام الأجزاء. في بعض التطبيقات، يمكن إضافة صبغات إلى الطلاء على جسم المقاومة الحرارية للحصول على لون محدد. يتم عادةً إضافة نقاط الألوان إلى المقاومة الحرارية باستخدام عملية التشرب. استخدم قلمًا لتوليد علامات تتطلب شخصيات أبجدية رقمية. تستخدم هذه الآلة حبرًا دائمًا فقط لوضع العلامات على الأجزاء. يجف الحبر عند درجة حرارة مرتفعة.
14. الفحص النهائي
ستخضع جميع الطلبات المكتملة لفحص العيوب الجسدية والكهربائية بناءً على أساس 'عدم وجود عيوب'. يتم فحص وتسجيل جميع المعايير قبل مغادرة المنتج المصنع.
15. التعبئة والإرسال تُعبأ جميع مقاومات الحرارة والمكونات بعناية وسيتم استخدامها من قبل العملاء.